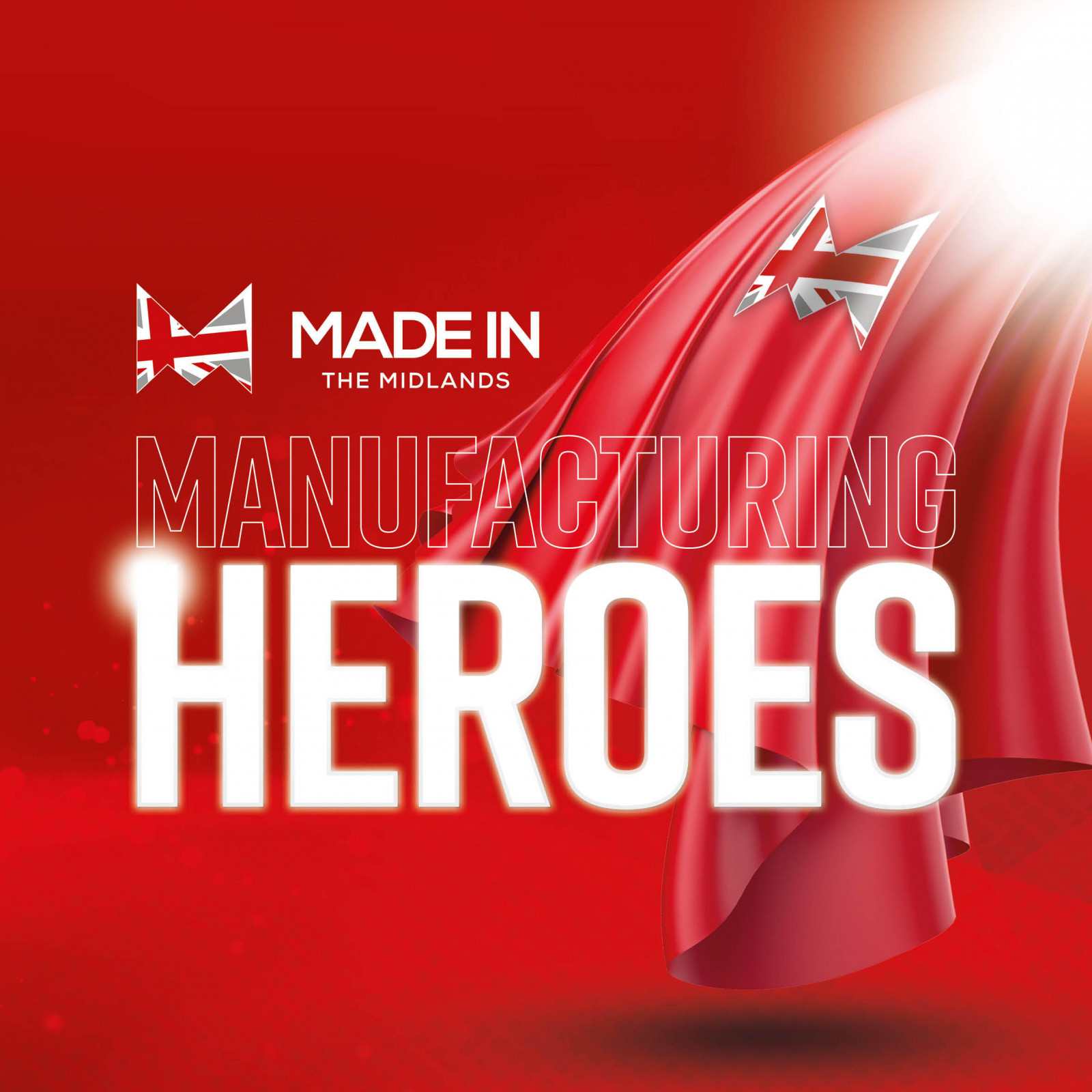
Rutland Plastics is a Manufacturing Hero
Rutland Plastics has been recognised as a Manufacturing Hero by the Made In Group. Made in the Midlands (#MiM) has been shining a light on businesses like ours for innovating, adapting and contributing to the pandemic response.
Rutland Plastics' largest contribution to the national response was the production of face shields. While Oakham School in Rutland was closed during lockdown, staff used 3D printers and laser cutters from the Design and Technology Department to begin making face shields. They approached Rutland Plastics to help boost productivity, which took them from manufacturing just a handful a day, to 8,000 a day. We were originally asked to 3D print a number of headbands for the shields, but soon decided it would be more efficient to manufacture a mould tool ourselves and then injection mould the plastic product from it.
We received the initial design for the 3D printed product from Oakham School and modified it in VISI to optimise the design for injection moulding. Once that was completed and approved, we designed the tool using a Meusburger bolster with aluminium bolster plates. The design then went into the toolroom and was milled on our Mazak VCN 530C CNC machine. The process from taking in the initial 3D design, through turning it into a mouldable product and finalising the mould tool took less than a week.
The two-impression mould was setup on one of our 80-tonne Engel moulding machines, both parts of the headband were formed from a medically-accredited polypropylene every 24 seconds during the production run of 40,000. Rutland Plastics covered the cost of production of the headbands and the cost of the production of the mould tool. To complete the full screen face shields, Oakham School arranged for the headbands to be attached to plastic visors, which were then distributed to front line NHS staff and key workers at hospitals, doctors surgeries, care homes and specialist schools.
Medical products are part our portfolio, we hold medical standard ISO13485, so we remained fully open during the Coronavirus lockdowns. We extended our output with additional components aimed at fighting COVID-19 some of which were used in the Nightingale hospitals. We were also part of a national consortium geared up to increase the manufacture of ventilators, and have taken delivery of a mould tool from Taiwan, moulding ventilator front covers from ABS thermo plastic polymer.
Our efforts during 2020 were also recognised by our local MP who nominated us a 'a local hero' and we were also featured on the local BBC news. Rutland Plastics is still a family owned business, we have been part of the local community for over 60 years, and so it was an easy decision to make to get involved with the community effort. We are very proud to have been able to help the local and national response to the Covid pandemic.
RECENT POSTS
Free design guide
"*" indicates required fields