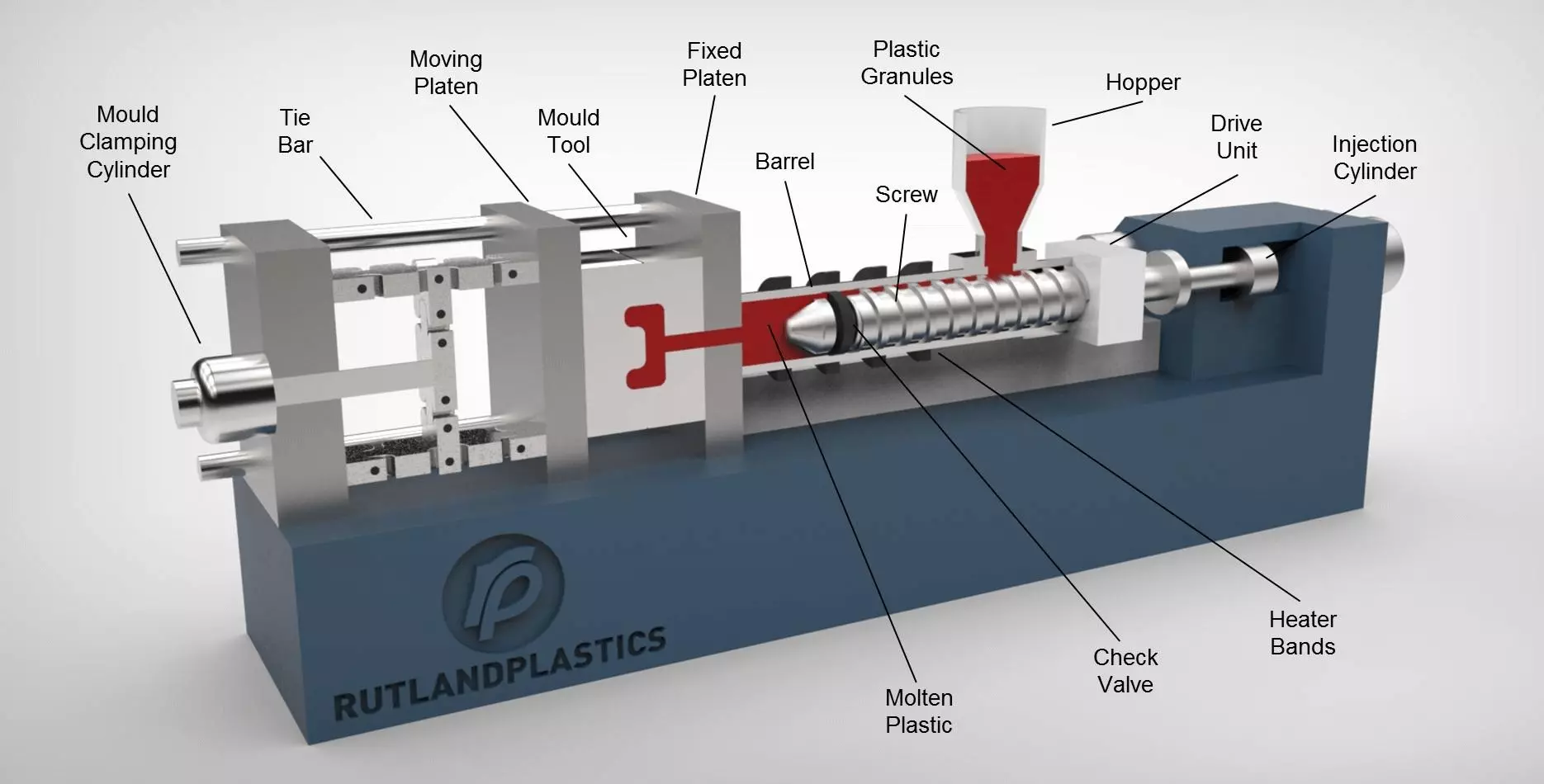
Plastic injection moulding is a manufacturing process that involves injecting molten plastic material into a mould cavity to create a desired shape. Here are the basic steps involved in the plastic injection moulding process:
Mould Design: The first step is to design a mould that will be used to create the desired part. The mould is typically made from steel or aluminium and is precision-machined to ensure accuracy. The mould design takes into account the desired shape, dimensions, and any additional features of the part.
Material Selection: Next, a suitable thermoplastic material is selected for the injection moulding process. Factors such as strength, flexibility, temperature resistance, and other requirements of the final part influence the choice of thermoplastic.
Material Melting: The selected plastic material is fed into the injection moulding machine's hopper. Inside the machine, the material is gradually heated and melted, typically using a heating barrel and an Archimeadean screw mechanism that pushes the material forward.
Injection: Once the molten plastic reaches the desired temperature and consistency, it is injected into the mould through a nozzle. The mould is clamped closed. The clamping force is usually expressed in tonnes and helps to define the size of the moulding machine. The molten plastic is forced into the cavity under high pressure which ensures that the material fills all the cavities of the mould taking on its shape and avoiding voids.
Cooling and Solidification: After the mould is filled, the molten plastic is allowed to cool and solidify inside the mould. The cooling process can be accelerated through the use of cooling channels or by circulating cool air or water. The cooling time depends on the material, part thickness, and design complexity.
Ejection: Once the plastic has solidified and reached the desired strength, the mould is opened, and the part is ejected. Ejection can be facilitated by ejector pins, air blasts, or other mechanical methods. The part is then separated from the mould, and the mould is ready for the next injection cycle.
Post-Processing: Depending on the specific requirements, the injection-moulded part may undergo post-processing operations such as trimming excess material, removing sprues and runners (the channels through which the plastic flowed into the part), adding surface finishes, or assembling multiple parts together.
Repeat Cycle: The entire process is repeated for the production of subsequent parts. The time needed to complete all steps of the production process is called the cycle time. Injection moulding machines can operate continuously, allowing for high-volume production.
It's important to note that the exact details of the injection moulding process can vary based on the specific machine, material, and part requirements. However, the general steps outlined above provide a good overview of how plastic injection moulding works.
RECENT POSTS
Free design guide
"*" indicates required fields