DESIGN FOR APPEARANCE
Although design contributes a great deal to the appearance of a part, the material also has a bearing. Filled polymers tend to have a poor surface finish when compared to their unfilled equivalents. However, assessment of what is aesthetically pleasing is to some extent subjective.
Related articles in this series:
Design for Economy
Design for Recyclability
Design for Time
Design Summary
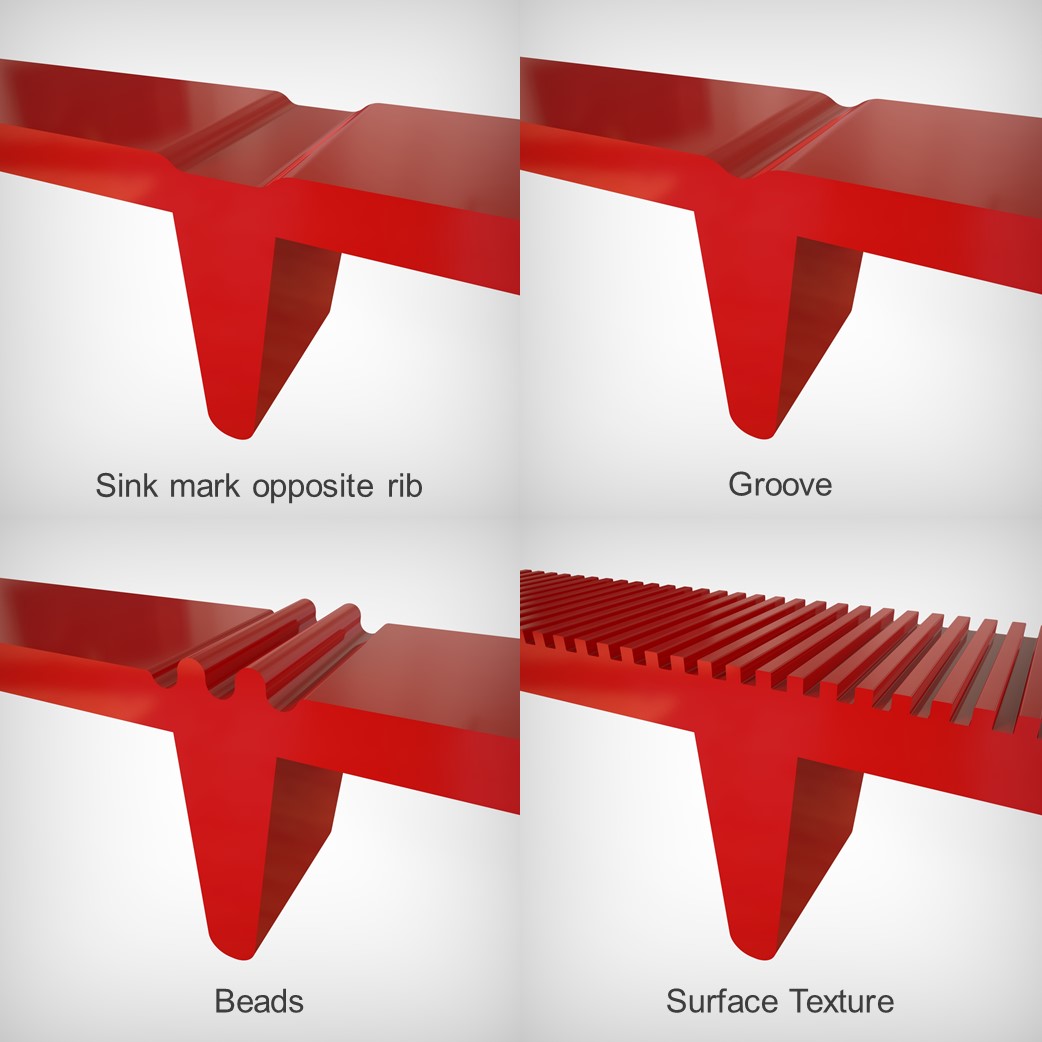
Various surface defects can occur
SINK MARKS
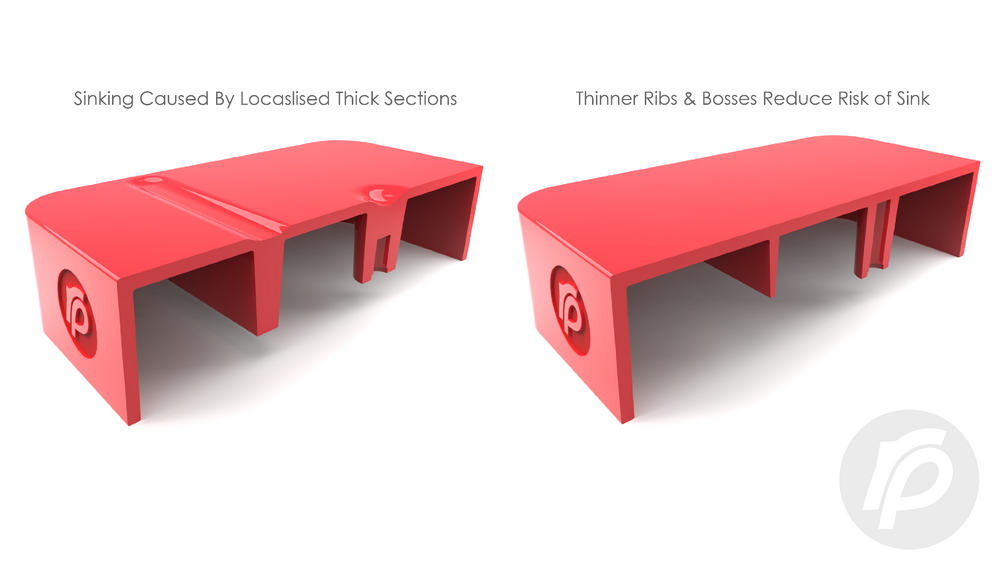
These typically occur over projections such as ribs or bosses. They are caused by localised thickening of the sections which results in an above average shrinkage. To minimise, attempts should be made to keep the thickness of ribs or bosses to 50% of that of the main wall. In certain circumstances, gas assisted moulding may be used to minimise the effect such as in the case of TV surrounds. Sink marks may also be disguised by the use of a textured surface or a styling feature e.g grooves, beads and surface texture as shown above.
WELD LINES
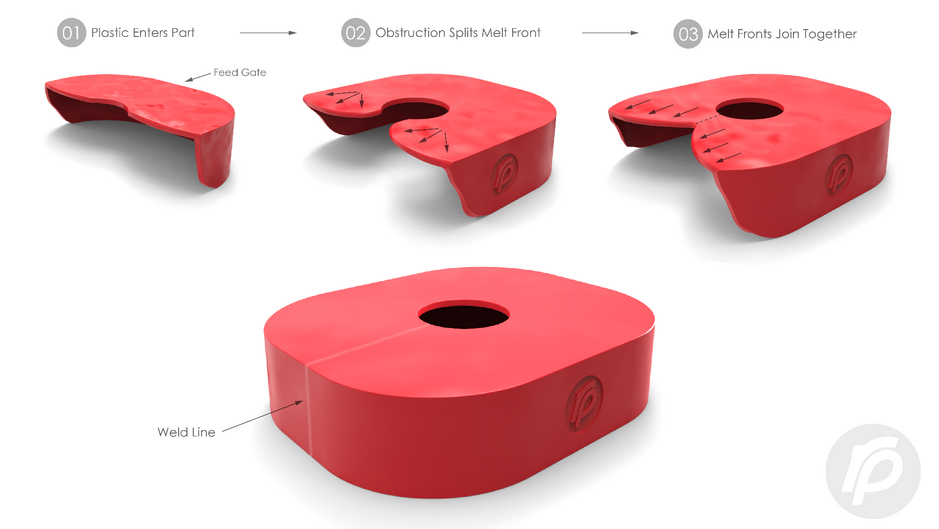
These occur where two flow fronts meet. Tool design can be critical in minimising the effect of these. Problems occur when there are holes in the component as the material has to flow around these and weld on the other side. In this instance, there are not only small weld lines adjacent to the hole but there may also be flow lines where the smooth passage of the material has been interrupted. Weld lines can cause a physical weakening because the joint at the weld is usually weaker. They look like cracks on the surface of a moulded part.
BURNING
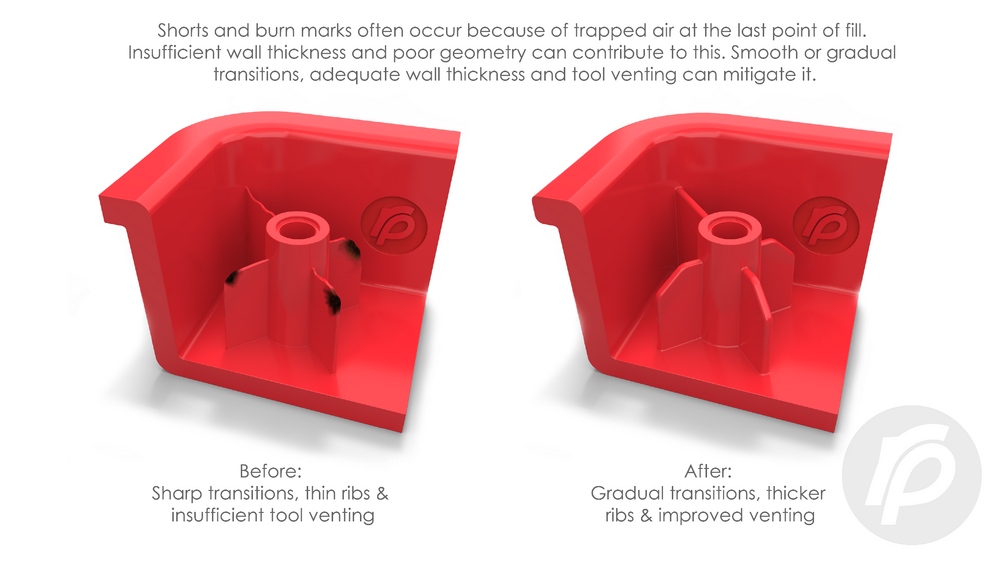
This occurs where there is insufficient venting at the edge of a moulding, as a result, burn spots develop due to diesel effects. Air traps may also occur around ribs or sharp transitions – venting is then required around ejector pins or in some other way. Smoother transitions rather than sharp corners or steps can also alleviate the problem.
VOIDS
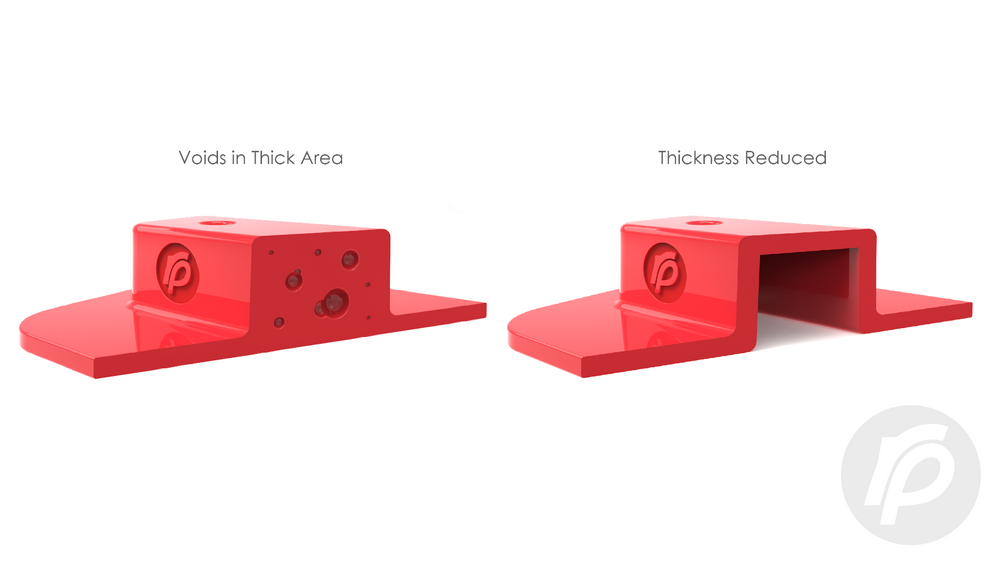
Air bubbles forming in the material due to thick sections. They are only visible in clear materials (unless they are particularly bad and break through to the surface) although they could well be present in any. This could lead to a weakening of the component. They are caused by excessive shrinkage. Wherever possible, excessively thick sections should be avoided. Also, some materials are more prone to voids. Rutland Plastics – is a specialist in thick section moulding and has several examples of void-free thick section mouldings (up to 110mm in one case).
There are other problems such as streaks, delamination, jetting and gate marks which are more the concern of tool designer rather than the product or component designer. Rutland Plastics can take your component design and advise on any necessary changes, tool design and manufacture is then managed in-house.
FURTHER READING OR LINKS TO ALL GUIDES?
- Design Guide
- Design Development
- Design For Appearance
- Design For Assembly 1
- Design For Assembly 2
- Design For Assembly 3
- Design For Cost Consideration
- Design For Economy
- Design For Mouldability 1
- Design For Mouldability 2
- Design For Mouldability 3
- Design For Precision
- Design For Recyclability
- Design For Stiffness
- Design For Strength
- Design For Time
- Design Summary
- Flame Retardancy
- Flexibility
Free design guide
"*" indicates required fields