ECONOMY
There are two areas to consider here:
Design of the part to minimise production costs
Design of the part to minimise tooling costs
The two can be connected and the decision over which route to follow will depend on the anticipated quantities required of the part. For the purposes of this article, we shall concentrate on production costs.
Related reading:
Design for Economy
Design for Recyclability
Design for Time
Design Summary
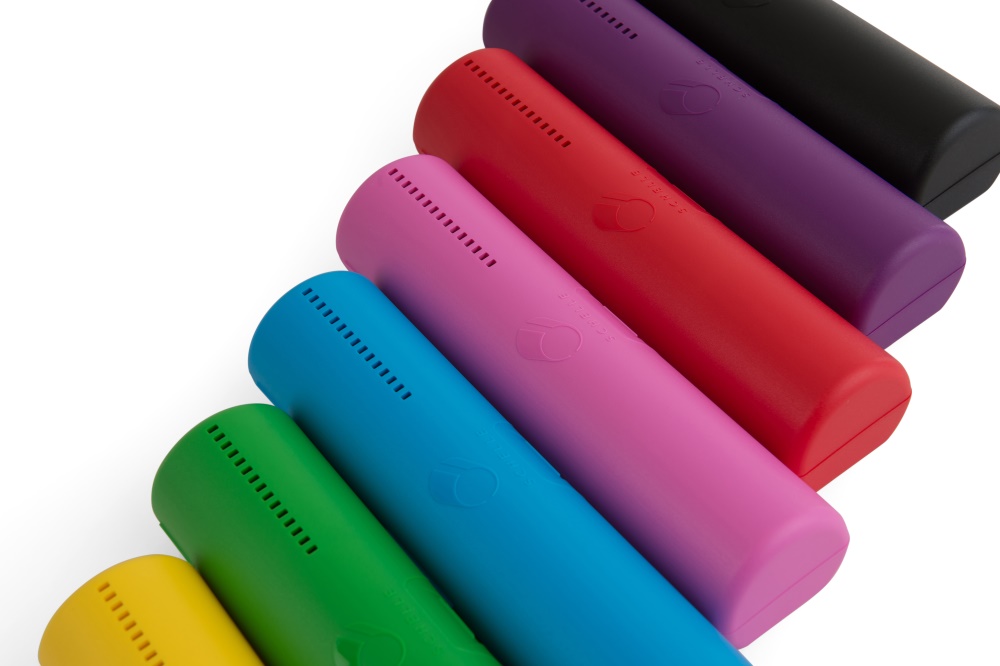
From a design perspective, injection moulding is a heat process and it takes time for parts to cool sufficiently to solidify before ejection from the mould. Put simply, the thicker the section, the longer the production cycle, the higher the cost. Therefore, the aim should be to keep sections as thin as possible and this will have the added benefit of less material content. Adding ribs rather than section is the preferred route if extra strength is required.
MATERIAL CHOICE
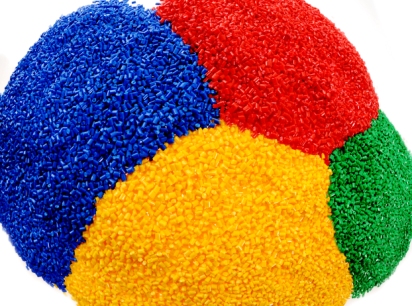
Another factor, of course, is the material selection. Thermoplastics can vary considerably in price from around £1 per kg for basic polyolefins up to £30 per kg and more for specialised polymers. Even within the more general ranges of commodity and engineering polymers, there is wide variation in price. The density of different polymers also varies leading to potentially heavier parts and higher cost.
This is an area where expert advice, such as that provided by Rutland Plastics, can be of benefit. Although it may be possible to design a part to use a cheaper material, e.g. polypropylene, by use of ribs and thicker sections, it may actually work out cheaper to use a stronger but more expensive material, such as nylon or ABS. Fewer ribs may then be required and the part could have thinner sections.
Material data sheets can only be of limited use here with strength and stiffness key properties as outlined in previous articles. It is far better to be guided by expert advice from a moulder or material supplier with experience of a range of applications for different polymers.
TOOL DESIGN
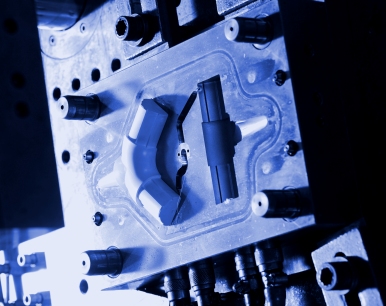
Injection mould tooling is relatively expensive but it is not always the case that injection moulding is only suited to high volume production. If it is possible to combine two or more parts into a single moulding, for example, then the cost of assembly and possible other ancillary parts can be saved making injection moulding a viable option.
It is also true that the simpler the mould tool the lower the cost. If possible design parts without holes in the side walls, undercuts and other complex features. If the part does need holes in the side then the decision on whether to mould these in or produce them using a secondary operation will depend on anticipated quantities of the part – the higher the number of parts required the more economical it becomes to have the moulded in.
FURTHER READING OR LINKS TO ALL GUIDES?
- Design Guide
- Design Development
- Design For Appearance
- Design For Assembly 1
- Design For Assembly 2
- Design For Assembly 3
- Design For Cost Consideration
- Design For Economy
- Design For Mouldability 1
- Design For Mouldability 2
- Design For Mouldability 3
- Design For Precision
- Design For Recyclability
- Design For Stiffness
- Design For Strength
- Design For Time
- Design Summary
- Flame Retardancy
- Flexibility
Free design guide
"*" indicates required fields