LONG GLASS FIBRE FILLED POLYMERS
When looking at metal replacement, for example, one of the issues of using plastic may be stiffness. One means of achieving a stiffer material is to add glass fibres. As well as increased stiffness the addition of glass fibres can also increase resistance to heat distortion and improve dimensional stability.
Please Note: This page is for information purposes only. Rutland Plastics is an Injection Moulder and does not supply polymers.
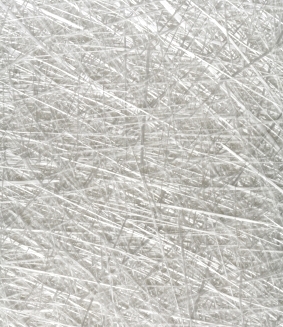
Conventional glass filled polymers, such as nylon and polypropylene for example, use glass fibres of about 3mm in length. Although this does improve the properties outlined above, there will be gaps in the web of glass fibres in the moulded part. For improved properties, there are long glass fibre filled reinforced grades of polymer available with strands the length of the plastic pellet – 12mm or more in some cases. Although the injection moulding process will break some of the fibres the finished part still shows considerable improvement in tensile and flexural strength, and an impact resistance up to 5 times better than the standard glass fibre filled grade.
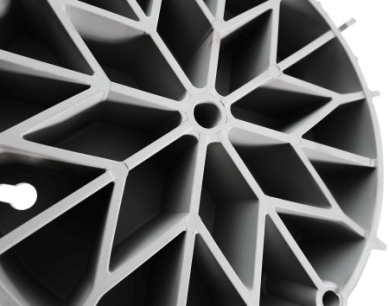
Although more expensive, the improved properties available can make the difference between using plastic or metal. It can also mean that the part could be designed with thinner wall sections so saving on weight and cycle time. In these instances, the premium for using long glass fibre filled material may be almost cancelled out by the cost saving.
Long glass fibre reinforced polymers also offer a cost saving when switching from a more expensive polymer, for example from standard glass filled nylon to long glass fibre filled polypropylene. The lower density means a lighter weight part and less material weight means lower cost, with the added benefit that the base polymer is also cheaper.