POLYMER THERMAL TESTING (PART 2)
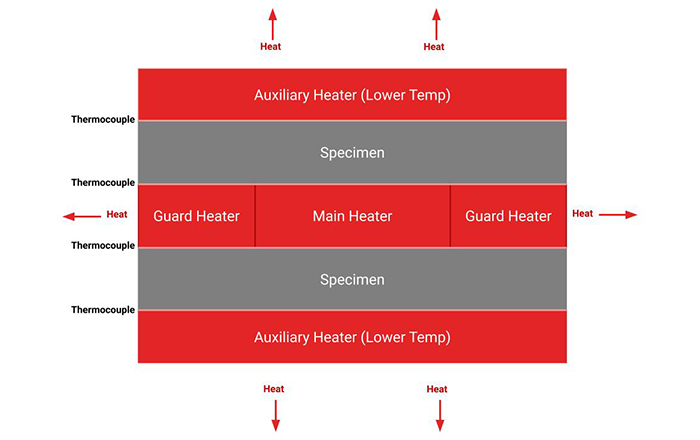
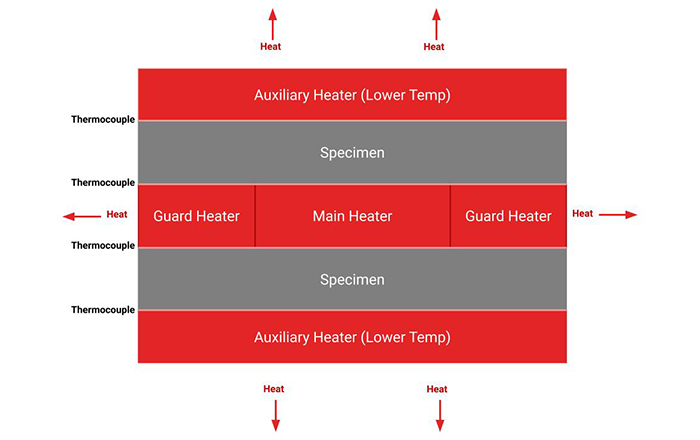
THERMAL CONDUCTIVITY
Thermal conductivity is measured to calculate the thermal insulating capacity of a plastic material.
Testing is carried out using heated platens with insulation around the sides to prevent radial heat loss. The main heater and guard heaters are kept at the same temperature and the auxiliary heaters at a lower temperature. Heat sinks are placed against the surface of the test plaques and the axial flow of heat is measured.
The applicable standards are ASTM E1530 (USA) and ASTM C177 (Europe).
RELATIVE THERMAL INDEX
This was formerly known as the Continuous Use Temperature Rating (CUTR). The Relative Thermal Index (RTI) is the maximum service temperature at which the critical properties of a material will remain within acceptable limits over a long period of time.
The applicable standard is UL 746B which specifies three ratings assigned to a material:
- Electrical – measuring dielectric strength
- Mechanical with Impact – measuring tensile impact strength
- Mechanical without Impact – measuring tensile strength
These three properties are calculated to be the most sensitive to high temperatures.
The performance of the material being tested is measured against a control material which exhibits good performance, hence Relative Thermal Index. Ideally the test material would be aged at normal operating temperatures for a long period of time but this is clearly not practical. Accelerated ageing is therefore achieved by using much higher temperatures.
Samples of both the test and control materials are placed in ovens at a constant temperature. Samples of both materials are removed at set times and tested for the above mentioned properties. By measuring these as a function of temperature and time, the theoretical end of useful service may be calculated. End of service life is defined as the time at which a material property has declined to 50% of its original value.
The standard that is applicable is UL 746B
Letter Code | Temperature (°C) | Load (kg) |
---|---|---|
A | 250 | 2.16 |
B | 150 | 2.16 |
D | 190 | 2.16 |
E | 190 | 0.325 |
F | 190 | 10.00 |
G | 190 | 21.60 |
H | 200 | 5.00 |
M | 230 | 2.16 |
N | 230 | 3.80 |
S | 280 | 2.16 |
T | 190 | 5.00 |
U | 220 | 10.00 |
W | 300 | 1.20 |
Z | 125 | 0.325 |
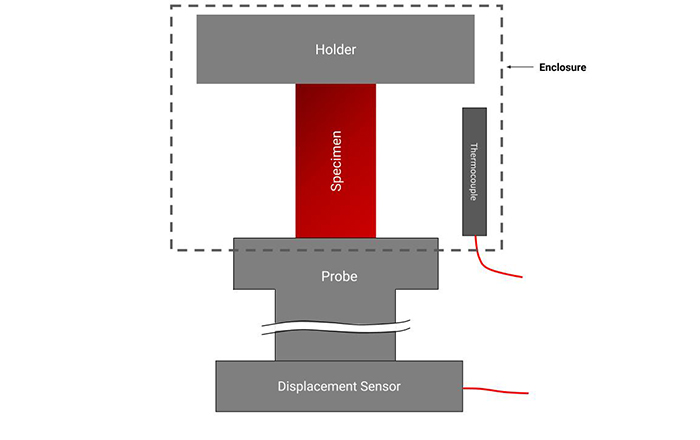
COEFFICIENT OF LINEAR EXPANSION
Any material expands when heated. The Coefficient of Linear Thermal Expansion (CLTE) is used to calculate changes in length, breadth and thickness of a moulded part with changes in temperature.
Addition of fillers, such as glass, significantly alters the CLTE of a polymer. Polymers may be formulated with CLTEs to match those of metal or other materials used in complex components, such as automotive parts.
With test method ASTM E631 CLTE is measured using a thermomechanical analyser. The sample is placed in an enclosure and is in contact with a probe leading to a displacement sensor. A small force is applied to keep the probe in contact with the sample. The temperature within the enclosure is raised at a rate of 5˚C per minute and the expansion of the sample is measured by the displacement sensor.
ASTM E631 covers temperatures between -120˚C and +600˚C.
ISO 11359 uses similar test apparatus but specifies a test temperature range of 23˚C to 55˚C.
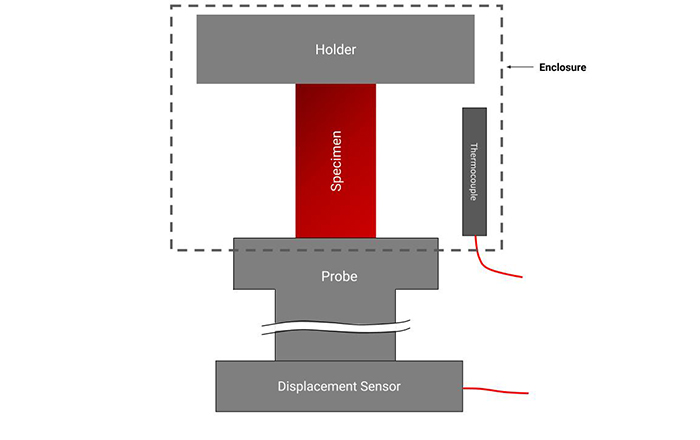
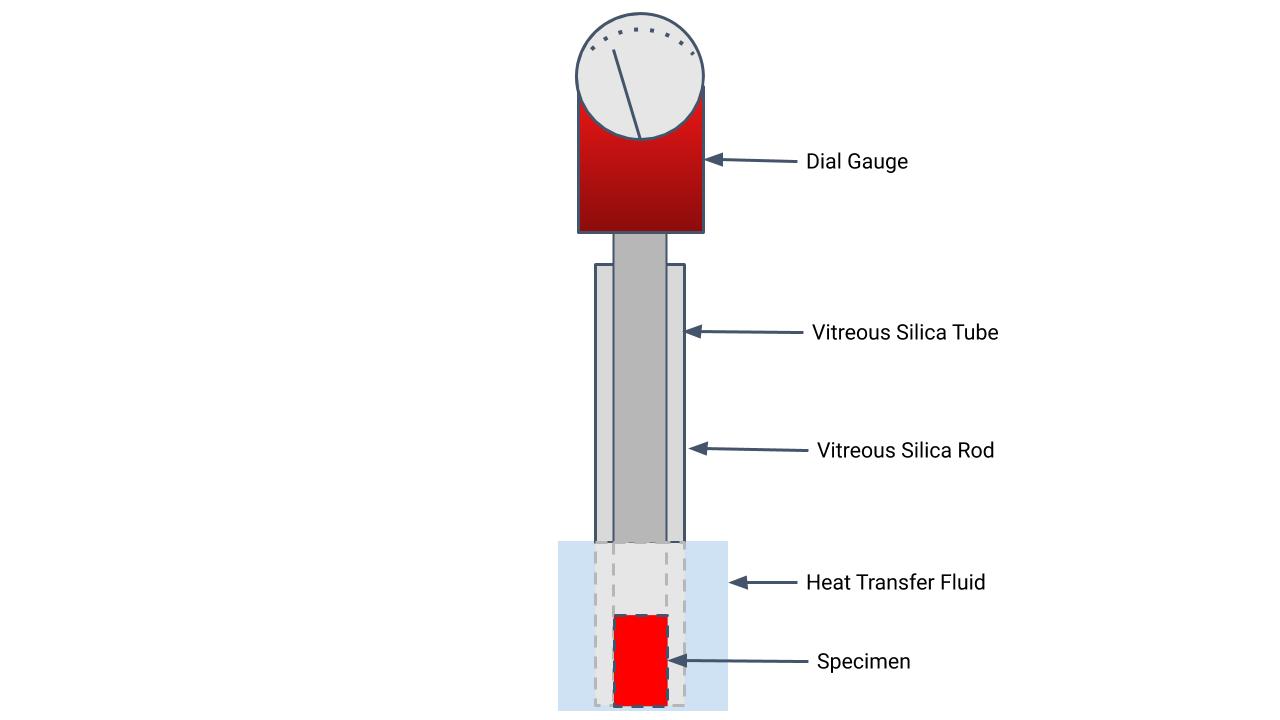
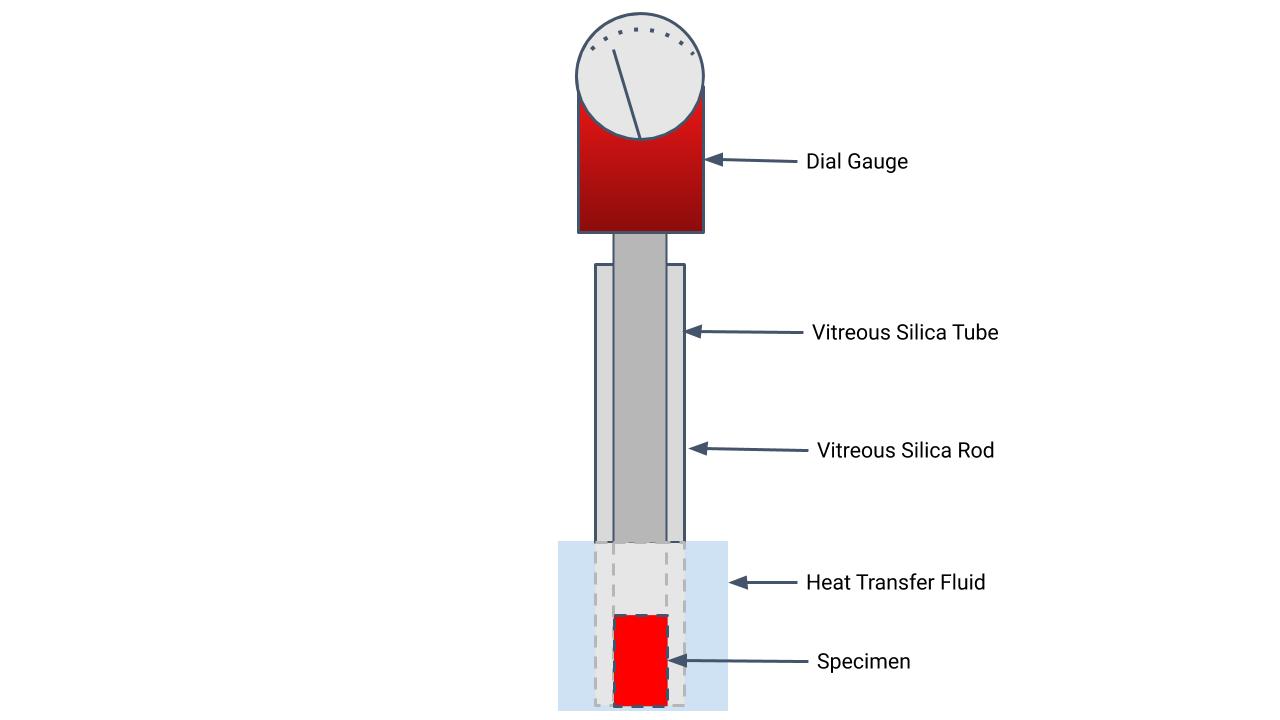
ASTM D696
ASTM D696 uses different test equipment – a silica dilatometer. A sample is placed into a silica tube and a silica rod with a gauge attached is inserted into the tube. The end of the tube containing the sample is placed in a bath at a constant temperature of -30˚C. Once the sample has reached this temperature, indicated by no movement in the gauge, the bath is replaced by one at a constant temperature of +30˚C. Once the specimen has reached +30˚C the bath is once again replaced by one at -30˚C. When the sample reaches -30˚C it is removed and measured at room temperature.