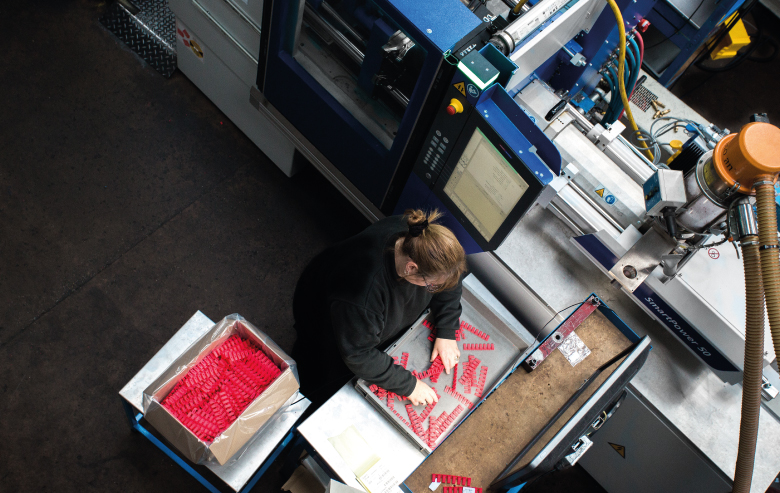
As with all manufacturing processes, common injection moulding defects can occur, with the right design for manufacture from the start, these issues can be prevented. Involving Rutland Plastics at an early stage can allow concurrent design engineering to take place reducing the time and resources needed to produce a successful design.
Sink Marks
These typically occur over projections such as ribs or bosses. They are caused by an above-average shrinkage associated with localised thick sections. An attempt should be made to minimise thick sections and reduce the thickness of features that interact with the main surface. Sink marks to a certain extent can be disguised by the use of a textured surface or a styling feature e.g. grooves, beads and surface texture.
Voids
Voids are air bubbles forming in the material due to thick sections. They are only visible in clear materials (unless they are particularly bad and break through to the surface) although they could well be present in any material. Voids may have a severe impact on the structural performance of the part. They are caused by excessive shrinkage. Wherever possible, excessively thick sections should be avoided and a uniform thickness should be used. Also, some materials are more prone to voids. Rutland Plastics is a specialist in thick section moulding and has several examples of void-free thick section mouldings.
Weld lines
These occur when two or more flow paths meet during the filling process. They can be caused by obstacles such as holes in the component as the material has to flow around these and weld on the other side. In this instance, there are not only small weld lines adjacent to the hole but there may also be flow lines where the smooth passage of the material has been interrupted. Weld lines can cause physical weakening because the joint at the weld is usually weaker. They look like cracks on the surface of a moulded part. Tool design can be critical in minimising the effect of weld lines.
Burning
This occurs when there is insufficient venting in the mould tool, as a result, air is trapped and overheated by compression resulting in burn spots. Air traps may also occur around ribs or sharp transitions – localised venting is then required. Smoother transitions rather than sharp corners or steps can also alleviate the problem.
There are other common injection moulding defects such as streaks, delamination, jetting and gate marks which are more the concern of the tool designer rather than the product or component designer. Rutland Plastics can take your component design and advise on any necessary changes with the tool design and the manufacture is then managed in-house. With over 65 years of experience in injection moulding, we have expert knowledge of every aspect of plastic injection moulding. We have created our own design guidelines to help with the design for manufacture process and is available on our website.
RECENT POSTS
Free design guide
"*" indicates required fields