DESIGN FOR STRENGTH
Designing for strength can be defined as:
“The maximum load that can be applied under certain conditions without causing failure to the part. Failure could be deformation, breakage or perhaps cracking, it would depend on the application.”
FACTORS AFFECTING PERFORMANCE
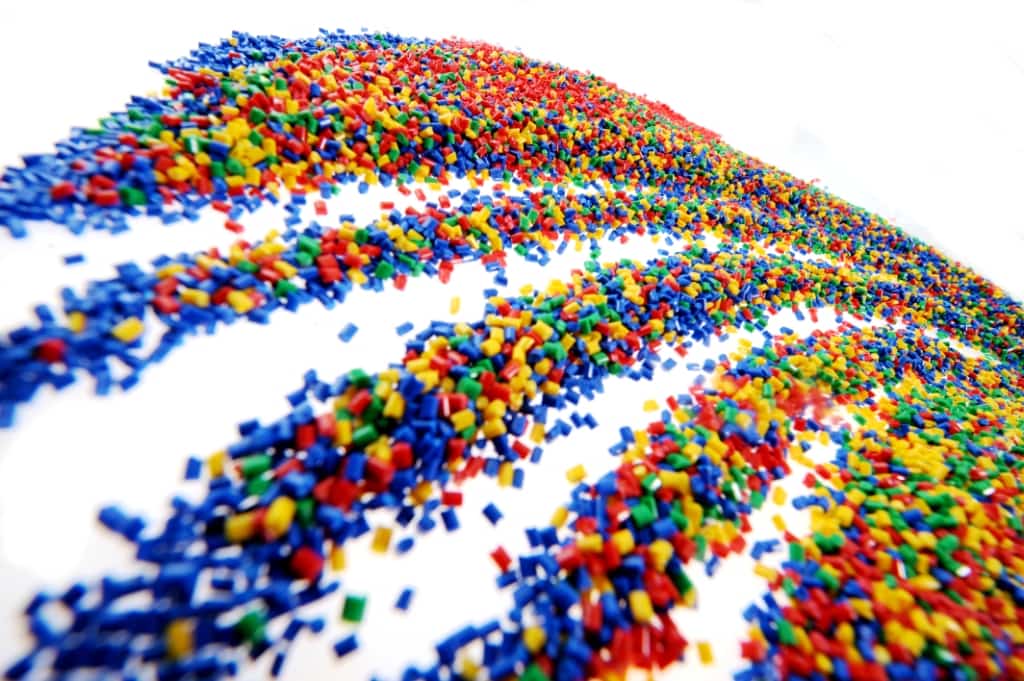
As described under ‘Designing for Stiffness’, filled materials perform differently to unfilled and temperature has a bearing on performance also. Adding glass fibres will strengthen a material but also make it more brittle. Whereas an unfilled material is likely to bend at its limit a glass filled material is more likely to crack or snap.
With regards to temperature, extremely low temperatures will make a material more brittle whereas it will become softer and more ductile at higher temperatures. The relative strengths and tolerance of temperature extremes will vary from one material to another. When looking at replacing metal parts, for example, with a plastic moulded component, direct comparisons of materials are not possible. For instance, the tensile strength of a non-plastic material is similar across the normal temperature range. For most thermoplastics the tensile strength will vary greatly with temperature changes.
Material performance can also be affected by chemicals, moisture and exposure to UV light.
TYPE OF STRENGTH REQUIRED
Part strength can mean different things subject to the conditions under which it is required to function. Ultimate strength could be based on the load a part is expected to carry – for example a plastic chair. This part would be tested well beyond what might be considered its maximum potential load to ensure that it would not fail.
It may be that strength relates to deformation where no or very little deformation of a part is permitted. For example, a clip for retaining the cable of, say a vacuum cleaner. This needs to ‘deform’ enough to enable the cable to be removed and replaced but permanent deformation would render it useless.
For plastics parts the nature of stress is an important consideration. Plastic parts have a ‘memory’, that is to say that if the stress is applied for a relatively short period of time the part will return to its original shape once the stress is removed. However, if the part is stressed for a long time then ‘creep’ occurs – when the stress is removed the part will not return to its original shape.
IMPACT STRENGTH
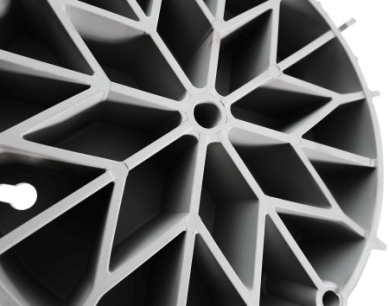
A final consideration is the toughness of the part which could relate to the impact it has to withstand. For instance, car bumpers should flex and withstand low speed impact – typically less than 5mph, to avoid damage in a parking accident for example. This is an area where fillers can considerably increase the impact strength of a material.
Various factors affect impact performance:
- Type of material
- Wall thickness
- Geometric shape
- Temperature – the range it is required to work in and how long at extremely high or low temperatures. Lower temperatures tend to make materials more brittle
- Weight of loading
- Exposure to chemicals. Some plastics are vulnerable to attack by cleaning fluids, etc. It may be necessary for the product or component to be resistant to even more hostile chemicals
- Flame retardancy
- Exposure to UV light
CONCLUSIONS
Once the particular type of strength requirement is defined it is then possible to identify a suitable material and design the part accordingly.
Design considerations for strength:
- Avoid sharp corners or notches, sharply angled wall intersections, large variances in sections and holes or inserts in the surface
- Avoid situations where the part could be overloaded – over-tightening plastic threads for example
- Ensure a good margin of safety as it is not possible to control all aspects of production and use. Also consider the worst case scenario for part failure
FURTHER READING OR LINKS TO ALL GUIDES?
- Design Guide
- Design Development
- Design For Appearance
- Design For Assembly 1
- Design For Assembly 2
- Design For Assembly 3
- Design For Cost Consideration
- Design For Economy
- Design For Mouldability 1
- Design For Mouldability 2
- Design For Mouldability 3
- Design For Precision
- Design For Recyclability
- Design For Stiffness
- Design For Strength
- Design For Time
- Design Summary
- Flame Retardancy
- Flexibility
Free design guide
"*" indicates required fields