BIOPLASTICS EXPLAINED
Bioplastics refer to a large family of plastics which are either sourced from biomass at the beginning of their life (bio-based), or that can be metabolised into organic biomass at the end of their life (biodegradable) or have both properties.
Examples of biomass used in bioplastics include corn, sugarcane, tapioca, or other forms of cellulose. Bioplastics have the same properties as conventional plastics and offer additional advantages such as a reduced carbon footprint or additional waste management options for example composting.
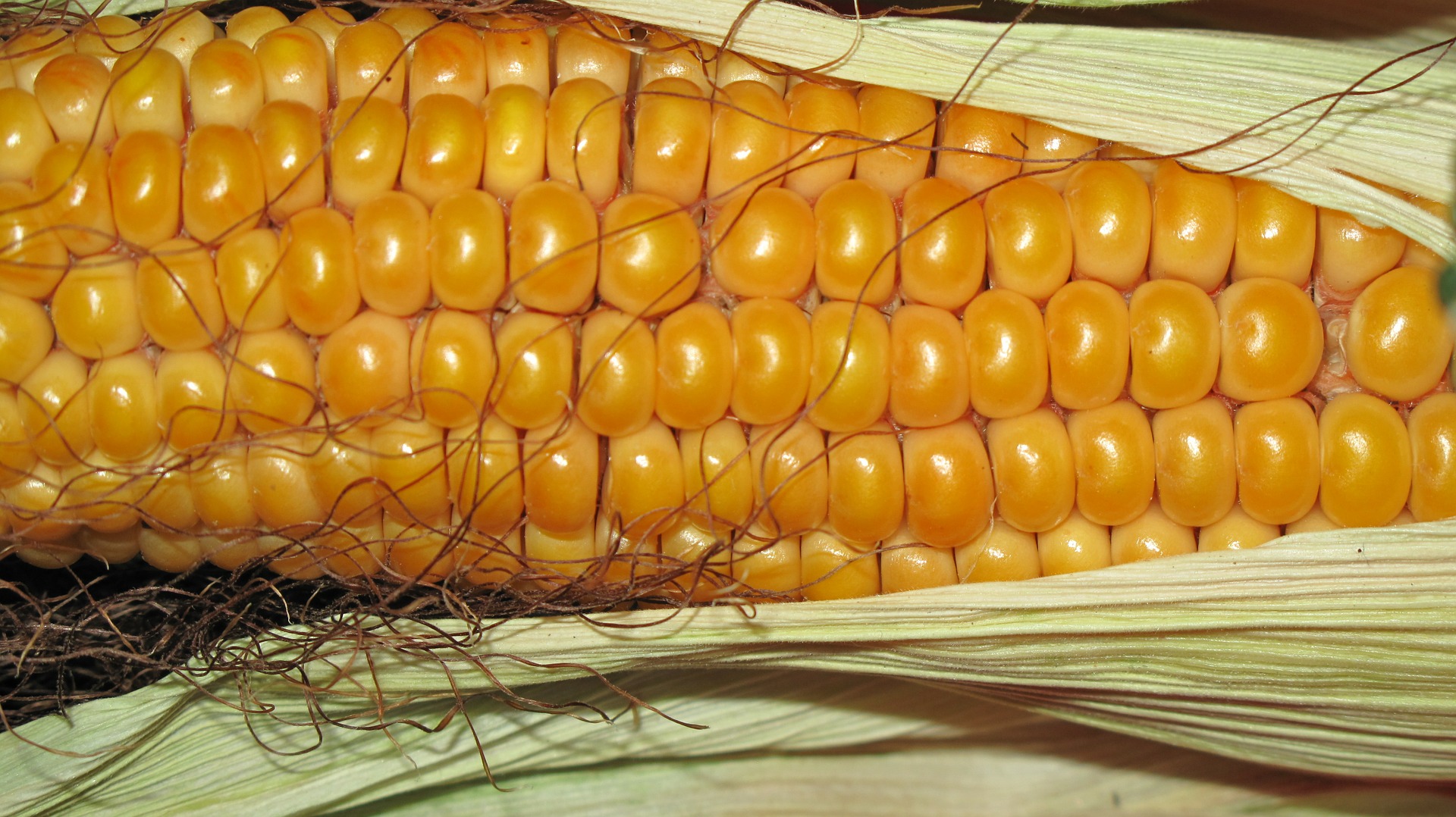
HOW IS BIOPLASTIC MADE
Bioplastic is made by extracting sugar from plants like corn, sugarcane etc. to convert into polylactic acids (PLAs), or it can be made from polyhydroxyalkanoates (PHAs) engineered from microorganisms (in simple terms: bacterial fermentation of sugar). PLA plastic is commonly used in food packaging while PHA is often used in medical devices like sutures and cardiovascular patches.
It is important to distinguish two aspects of bioplastics: biodegradable and compostable. Also, the composition and the end-of-life are independent aspects that should not be confused because bio-based plastics are not always biodegradable and biodegradable plastics are not always made from a renewable resource. It is worth noting that traditional plastics can be biodegradable.
Essentially, bioplastics are not made from petroleum but, and this is a crucial ‘but’, they must be disposed of at commercial composting facilities where the material can be heated to a temperature high enough to activate the microbes to break it down, otherwise they will function similarly to traditional petroleum-based (petro-based) plastic.
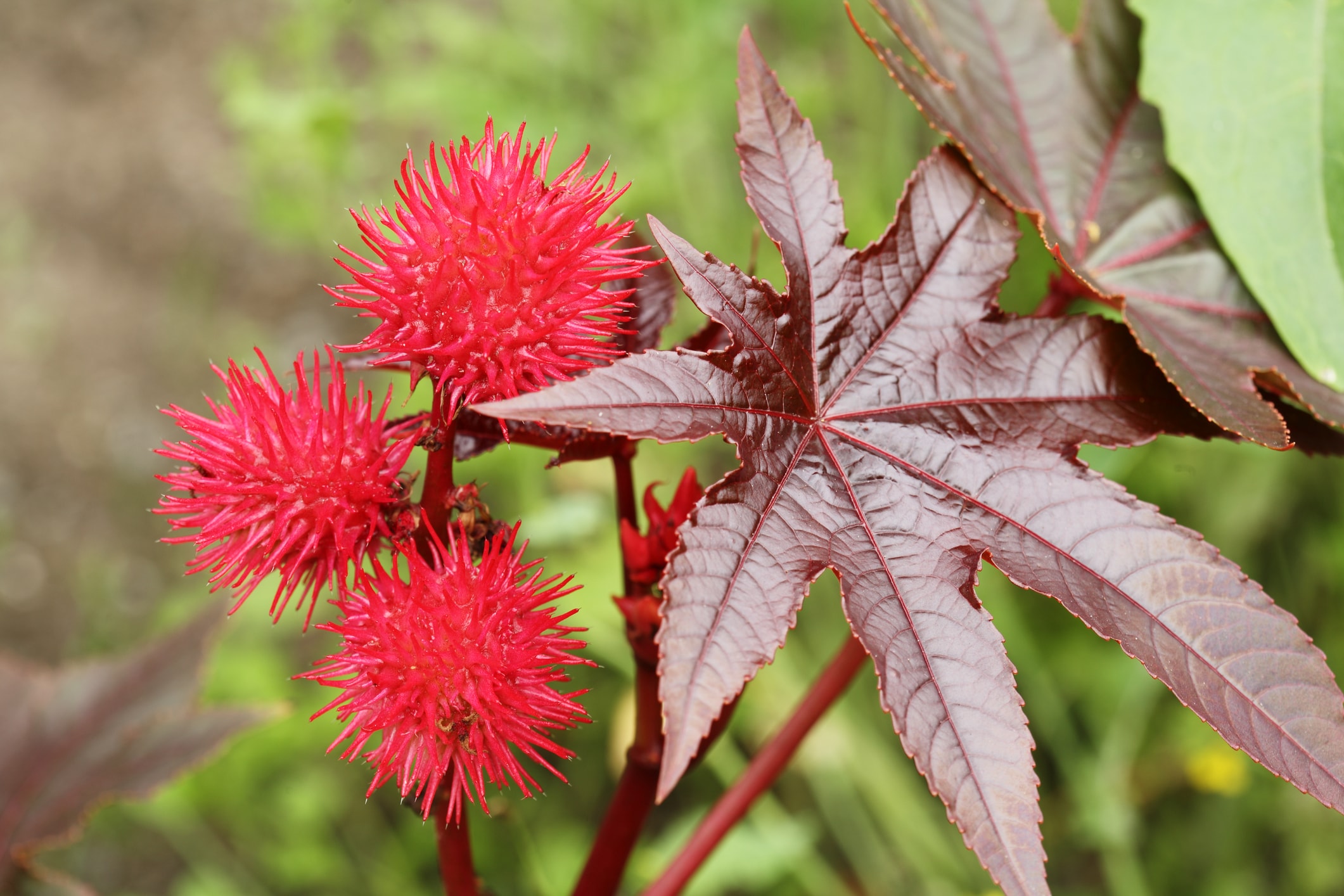
Material types – three main groups:
Biobased or partly biobased, non-biodegradable plastics such as biobased PE, PP or PET (so-called drop-ins) and biobased technical performance polymers such as PTT or TPC-ET.
Plastics that are both biobased and biodegradable, such as PLA, PHA or PBS.
Plastics that are based on fossil resources and are biodegradable, such as PBAT.
CHEMICAL RESISTANCE
DefinitionsDerivativeEnd of Life Options (EoL)
Bio-based or bioplastic | Derived from biomass/biological material (e.g. raw organic matter like starch or sugar contained in plants such as corn). | Two options dependant on the waste management structure locally available: 1. separated through various mechanical processes (sorting like many (but not all) petroleum-based plastics) at recycling centres after which the recovered plastic can be reused following processing (re-melting or granulation). 2. composted through an industrial biowaste collection and after recycling can be used as compost or renewable energy. *also see the biodegradable section below. |
Petrochemical/fossil | Made from fossil-based feedstocks e.g. petroleum or gas. | |
Renewable Feedstock | A feedstock that can be replenished on a human timescale (e.g. not a slow regeneration rate). | |
Renewable additives | Minerals, natural fibres, glass etc. | |
Biodegradable | Decompose by naturally occurring bacteria in the environment. There are normally two forms of biodegradable plastic, injection moulded and solid (solid forms are normally used for items such as food containers, garden refuse bags, and water bottles). | Biodegradable plastics do have some drawbacks, for example, they do not decompose unless they are disposed of properly, meaning that biodegradable plastics must be treated similarly to compost. The natural breakdown of the plastic will not occur if it is simply tossed in a landfill. |
Compostable | Compostable plastics are those plastics which have been tested and adhere to international standards. All compostable plastics are biodegradable, but not all biodegradable plastics would be considered compostable. |
Breakdown under commercial composting conditions. The material biodegrades in a certain period of time and leaves no toxic residue in the soil. |
Recycling | The reprocessing of used product materials into other products. | |
Carbon footprint | The total greenhouse gas emissions caused directly or indirectly by a person, organisation, event or product. | CO2e is calculated by multiplying the emissions of each of the six greenhouse gases by its 100 year global warming potential (GWP). |
Oxo-degradable | Are neither a bioplastic nor a biodegradable plastic but are conventional plastic mixed with an additive. | These additives catalyse the natural degradation process in the presence of oxygen to cause quick fragmentation into what is called microplastics. The process continues until it is no longer a plastic, and has become a biodegradable material. |
Biocomposite | Is traditional petro-based plastic that combines biomaterials (renewable fillers) like reclaimed wood, starch, flax, jute, hemp, and other similar materials. |
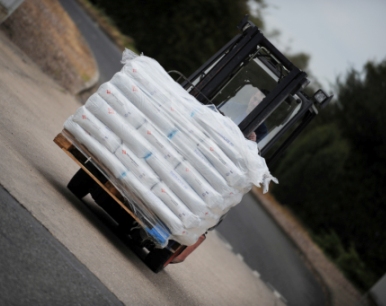
EXAMPLES OF ESTABLISHED BIOPLASTIC MATERIALS
BIOBASED, NON-BIODEGRADABLE POLYOLEFINS AND PET (COMMONLY REFERRED TO AS DROP-IN BIOPLASTICS)
Commodity plastics like PE, PP and PVC can also be made from renewable resources, most commonly from bioethanol. Bio-PE is already being produced on a large scale in Brazil 200,000T p.a. (corn starch). Bio-PP and Bio-PVC are soon to follow that trend. The partially bio-based polyester PET is used for both, technical applications and packaging (drinks bottles, such as cola bottles). Drop-in bioplastic is a “bio-similar” copy of petrochemical plastics but it is made from biomass instead of fossil-oil. Because drop-in bioplastics uses the same pathway as the petrochemical plastics, they have the advantage of immediate use in existing machinery and equipment without the need for investment or adaptation, and the testing period is also shorter.
BIOBASED, NON-BIODEGRADABLE TECHNICAL/PERFORMANCE POLYMERS
This large group comprises of many specific polymers, such as biobased polyamides (PA), polyesters (e.g. PTT. PBT), polyurethanes (PUR) and polyoxides. Their use is the most diverse. Some technical applications are textile fibres (seat covers, carpets), automotive applications like foams for seating, castings, cables, hoses, and covers etc. Usually, their operating life lasts several years. Therefore, they are referred to as durables, and biodegradability is not a sought after property.
BIOBASED, BIODEGRADABLE PLASTICS
This group includes starch blends made from thermo-plastically modified starch and other biodegradable polymers as well as polyesters such as polylactic acid (PLA). Unlike cellulose materials (regenerative-cellulose or cellulose-acetate), they have been available on an industrial scale only for the past few years. So far, they have primarily been used for single-use products such as packaging, but it is an innovative area of the plastics industry that continues to grow due to the introduction of new biobased monomers.
Several materials in this group, primarily PLA, are striking a new pathway from biodegradation and towards EoL solutions such as recycling. The renewable basis of these materials is now at the focus of attention and R & D. Government schemes and pilot projects aim to establish recycling processes and streams.
BIODEGRADABLE, FOSSIL-BASED PLASTICS
They are a comparatively small group and are mainly used in combination with starch or other bioplastics because they improve the application-specific performance of the latter by their biodegradability and mechanical properties. These biodegradable plastics are currently still made in petrochemical production processes. However, partially bio-based versions of these materials are already being developed and will be available in the near future.
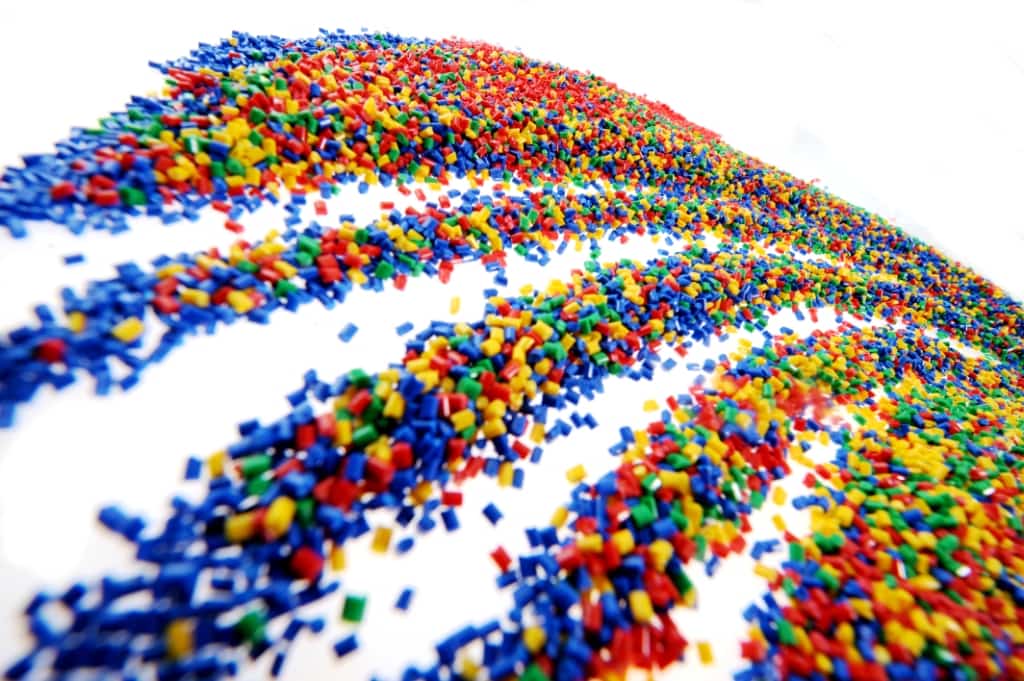
YOUR OPTIONS
As one of the country’s leading plastic injection moulders, we work with all the major polymer suppliers and so have access to a wealth of knowledgeable resource at our disposal to include up-to-date developments in materials. We are happy to discuss with you what you want to achieve and offer our advice on the best options to meet your requirements.
Sources:
National Geographic National Geographic
The hierarchy for waste minimisation as according to the Waste Framework Directive (2008/98/EC)/18/:
- PREVENTION in the form of waste reduction and should be achieved by developing clean technologies and processes that require less material in the end products and produce less waste.
- RE-USE is the second strategy and involves the collection and reuse of products and materials. Reuse also includes new uses for items that have served a purpose.
- RECYCLING involves processing and producing materials and products from waste (including composting and other biological transformation processes).
- ENERGY RECOVERY indicates the recovery of energy from the combustion of landfill gas or from the waste incineration.
- DISPOSAL is the least desirable option and shall be applied once waste cannot be treated in any other way.
Recommended reading:
TEDx – Plastic Rehab presented by Kim Ragaert
Bioplastic News – The Truth About Bioplastics
Carbon Trust – helping companies manage value chain carbon emissions