PLASTICS ADDITIVES – COLOURS AND SPECIAL EFFECTS
Please Note: This page is for information purposes only. Rutland Plastics is an Injection Moulder and does not supply plastics additives.
COLOURS
One of the great advantages of the majority of thermoplastics is their ability to be coloured. Although parts can be painted, as is often the case with body panels for cars, for example, a far better alternative is to colour the part itself. As the colour is present throughout the part it can never wear off.
Colours can also be matched to other objects, even if they are manufactured from a different material, or to match a corporate or brand colour. Colour is provided by the use of pigments. These are tiny particles which have to be mixed evenly in the polymer whilst it is in a molten state.
For the plastic moulder colour can be achieved via two main routes:
- Ready compounded material. A material compounder will colour the base polymer by extruding it with the required blend of pigments. This ready coloured material is then supplied in pellet form for the moulder to use
- Addition of colour in a carrier heavily loaded with pigments known as masterbatch. This may be supplied either in pellet or liquid form. In either case, they have highly concentrated levels of pigment which are then mixed with the base polymer at addition rates of typically 1%-4%. With the liquid form special dosing equipment is attached to the moulding machine. Pellets can either be added by automated dosing equipment on the moulding machine or mixed in with the base polymer manually before moulding in the usual way
Apart from the challenges of matching the colour of the plastic to a similar colour in another material, there is also the question of light. The colour of a plastic can appear different in different lights. That is to say, a plastic moulding that appears to match another part in tungsten light may not match in daylight or under fluorescent lighting. The challenge for the colourist is to find the right combination of pigments to achieve the colour match under all required light conditions. However, there are some colours where this is not achievable, fortunately this is rare.
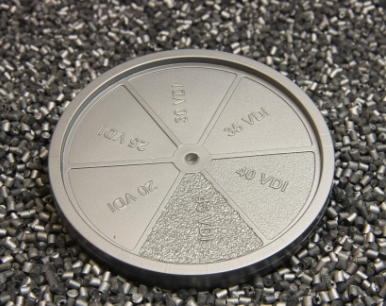
SPECIAL EFFECTS
As well as straightforward colours, a number of special effects are achievable in plastic by the use of masterbatches.
Metallic
Adds a shine and shimmer giving plastics the appearance of polished steel or brushed aluminium.
Sparkle
This may be achieved either by the inclusion of small metallic flakes or, for a more subtle effect, glass encapsulated pearlescent particles.
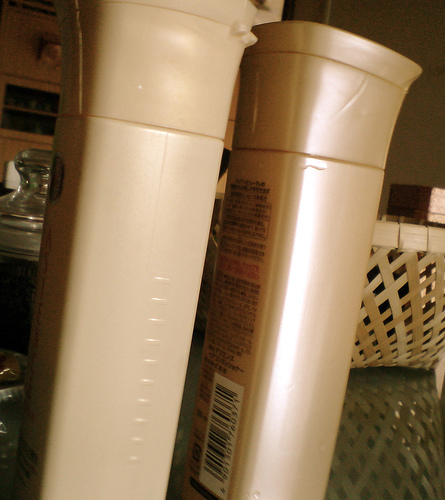
Pearlescents
Iridescent effect giving the lustre of pearls. Used regularly in containers for personal care products, such as shampoo.
Iridescent
Creates an illusion of depth by use of soft but intense colour visible at varying angles in a milky appearing compound.
Fluorescent
Intense, eye catching colours.
Glow in the Dark
The use of phosphorescent pigments to absorb light and then re-emit in the dark. A wide variety of colours is possible.
Photochromatic
Exposure to UV light results in a colour change from light translucent to deep colours.
Thermochromatic
Changes in temperature result in a change of hue. These can be tailored to change in either a hot or cold environment.
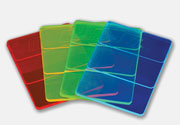
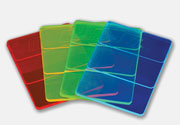
Edge Glow
Again for use with clear thermoplastics. These additives absorb light and re-emit in the energy in the form of longer wave lengths. The light reflects off the internal surfaces to create a glow effect on the edges.
Transparent
For use in clear thermoplastics, coloured tints of varying shades and intensity.
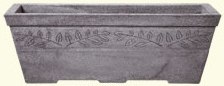
Granite/Marble
Stone effects can be achieved, among them granite and marble. Popular for garden planters, for example.
Wood Grain
Special moulding techniques are used to produce patterns similar to wood grain.
Tortoise Shell
Contrasting pigments are added to a colour base to create a shell-like appearance.
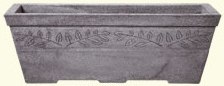