REACTION INJECTION MOULDING (RIM)
Please Note: This page is for information purposes only. Rutland Plastics is an Injection Moulder and does not offer RIM moulding services.
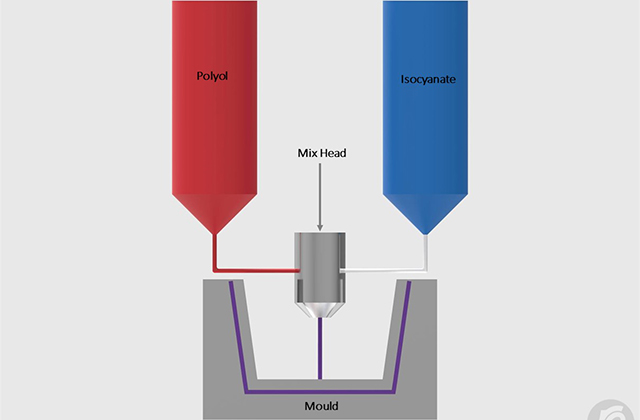
PROCESS
This is a form of injection moulding that produces components with a honeycomb like centre. It is a cold injection process that does not require pre-heating of moulds or post curing of parts. Two materials are mixed prior to injection; these materials react in the mould to form a solid moulding.
The low pressure process can produce large mouldings – up to 40kgs and in excess of 1m square with sections of 5mm-15mm. The resulting components have a high level of stiffness.
MATERIALS
This process uses a fast acting polyurethane resin.
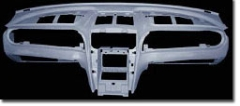
APPLICATIONS
Products manufactured using this process include:
- Business machine housings
- Point of sale display components
- Containers
- Pallets
- Office furniture
- Sporting goods
- Automotive
- parts
ADVANTAGES
- Low pressure mouldings mean the mould tools can be manufactured from silicone, resin, modelboard or aluminium resulting in cheaper tooling costs
- Fast tool manufacture
- High impact strength and dimensional stability
DISADVANTAGES
- Parts are more expensive as the surface finish is generally poor needing filling, sanding and painting. Generally a textured finish is used
- Slow cycle times
- Expensive raw materials