VACUUM FORMING
Please Note: This page is for information purposes only. Rutland Plastics is an Injection Moulder and does not offer vacuum forming services.


PROCESS
The vacuum forming process involves the heating of a sheet of plastic until soft and then draping it over a mould. A vacuum is then applied which sucks the sheet over the mould so forming the desired shape. Where the shape is more complex or has deep recesses a plug may be used to assist the pressing of the plastic sheet into the mould.
Once sufficiently cooled the part is then ejected and trimmed.
MATERIALS
A wide variety of thermoplastics are supplied as sheet and vacuum formed. The most widely used include ABS, PET, Styrene, Polycarbonate, Polypropylene, Polyethylene, PVC and Acrylic.
APPLICATIONS
- Baths and shower trays
- Yoghurt pots
- Boat hulls
- Machinery guards
- Refrigerator linings
- Parts of vehicle cabs
- Exterior signs
ADVANTAGES
- The low forming pressures means comparatively low cost tooling
- As moulds can be manufactured from inexpensive materials, tool manufacturing lead times can be relatively short
ADVANTAGES
DISADVANTAGES
- Secondary operations are usually required to trim the formed sheet into the finished part
- Uneven sections may result from the stretching process resulting in potential weak spots
- Inability to hold tolerances
THERMOFORMING
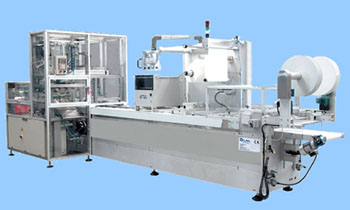
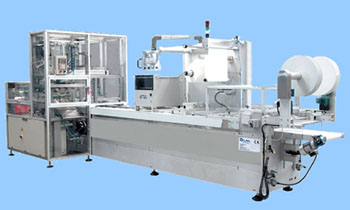
PROCESS
Thermoforming is very similar to vacuum forming but greater use is made of air pressure and plug assisted forming. Generally, this process has faster cycle times. The majority of thermoforming applications are high volume so roll fed machines are used. However, sheet fed machines may be used for lower volume products.
For very large volumes a fully integrated production line may be used with raw material being fed into a sheet extruder which in turn feeds the thermoformer.
The sheet is heated to soften and then moved to the mould tool. Air pressure and plugs form the sheet to the required shape. Another difference from vacuum forming is that many of the thermoforming tools also crop the part rather than using a secondary operation.
MATERIALS
The most commonly used materials include Styrene, Polypropylene, PET and PVC. Thermoforming is widely used for food packaging which requires barrier properties from the material to resist the passage of odours, moisture and gases. Therefore, a co-extruded material, i.e. a combination of two materials with one of them usually being Ethylene Vinyl Alcohol (EVOH), is used.
Food packaging is frequently decorated. This is achieved either by post mould printing or, more usually, placing pre-printed sheet into the mould cavities.
APPLICATIONS
- Food packaging including meat trays, ice cream and margarine tubs, sandwich packs
- Toiletries containers
- Pharmaceutical containers
- Blister packaging
- Point of sales display trays
ADVANTAGES
- Short lead times for tooling
- Ability to produce thin-walled parts
- Ability to produce large parts
- Faster cycle times than vacuum forming
DISADVANTAGES
- Limited shapes possible
- High scrap rates
- Only one side of the part can be defined by the mould
- As with vacuum forming there are variances in wall thickness
- Inability to hold tolerances