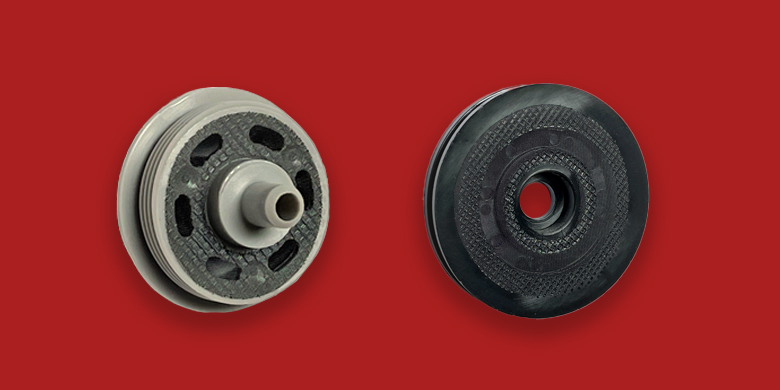
Plastic injection mouldings often need to be machined or assembled with other components to arrive at the final product. There are several methods of joining plastic available but sonic welding provides a quick, clean and efficient method of welding plastic parts together with a strong and permanent bond. There are a number of different friction welding methods: Ultrasonic welding, Vibration welding and Spin welding. All these methods work on the same simple principle of creating friction to create heat to melt the plastic at the joint.
Ultrasonic Welding is the most popular method and uses ultrasonic energy to create surface and intermolecular friction thus generating heat and in turn forming a weld. Ultrasonic welding is suitable for most thermoplastics. Amorphous polymers are generally ideally suited, semi-crystalline polymers, on the other hand, are generally more difficult to weld ultrasonically.
The suitability of a thermoplastic for ultrasonic welding depends on its ability to transmit high frequency vibration. This means that rigid materials are better than flexible ones. Melting behaviour is also important. Materials that melt over a broad temperature range and solidify gradually work best. The table shows the quality of weld to be expected when joining a particular thermoplastic to itself under optimum conditions. A near-field weld is one where the joint interface is within about 6mm of a welding horn tip contact point; anything else is far-field. Far-field welding is much less effective because of energy losses within the material.
The table below shows the ease of welding for different materials
Material |
Ease of Welding |
|
Near-Field |
Far-Field |
|
ABS |
Excellent |
Good |
Acetal |
Good |
Fair |
Acrylic |
Good |
Good to Fair |
Fluoropolymers |
Poor |
Ineffective |
PC/ABS |
Excellent to good |
Good |
Polyamide (Nylon) |
Good |
Fair |
Polycarbonate |
Good |
Good |
Polyester Thermoplastic |
Good |
Fair |
Polyethylene |
Fair to Poor |
Poor |
Polypropylene |
Fair |
Poor |
Polystyrene(General Purpose) |
Excellent |
Excellent |
Polystyrene (High Impact) |
Good |
Good to Fair |
Polysulphone |
Good |
Fair |
PPO |
Good |
Good |
PPS |
Good |
Fair |
Rigid PVC |
Fair to Poor |
Poor |
At Rutland Plastics, we have the expertise, flexibility and facilities to add the finishing touches required. Sonic welding is just one of the additional services we offer. We are also able to provide machining, gluing and multi-component assembly in addition to our full range of plastic injection moulding services.
RECENT POSTS
Free design guide
"*" indicates required fields