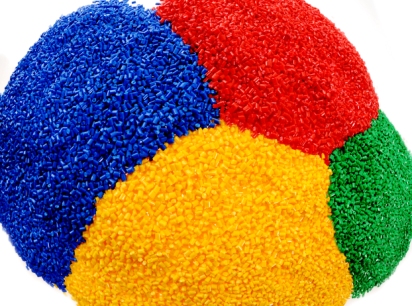
Rutland Plastics is one of the leading plastic injection moulding companies in the UK. There are other thermoplastic moulding solutions available that are suited to different applications and each have their own advantages and disadvantages. Rutland Plastics is a plastic injection moulding specialist. Some of the other moulding solutions available from other companies are outlined below.
Injection blow moulding is used for manufacturing large quantities of hollow parts, e.g. bottles, jars and other containers. Molten plastic is injected into a hollow, pre-heated mould which forms the external shape. This is clamped around a core rod which forms the internal shape. The mould opens and the core rod is clamped into a chilled blow mould. The core rod opens allowing compressed air into the perform inflating it to the finished shape. Once cooled the mould opens and the finished item is stripped off the core rod.
There are a number of different methods of compression moulding but the process is broadly the same. The most common method is Dough Moulding Compound or Bulk Moulding Compound. The preheated material is placed directly into a heated mould. The material is forced into all cavities when the mould is closed with a top force. Heat and pressure are maintained until the material is cured. Another method is Sheet Moulding Compound, this process involves placing a reinforcing material, such as glass fibres, between layers of a thermoplastic and heating the materials so as to bond them together into a single sheet of material. This is then cut to size and reheated before being placed in a compression moulding press. This has a higher cost due to the handling and manufacturing costs in making the sheet. The material used in making the sheet is also heated three times – when making the initial thermoplastic sheet, then again when bonding with the reinforcement and finally, when making the part itself.
Rotational moulding (also referred to as Rotamoulding or Rotomoulding) is used to produce hollow plastic products. It differs from other moulding methods in that the melting and moulding stages occur after the polymer is placed in the mould and no external pressure is applied. A predetermined amount of polymer powder is placed in the mould. Once the mould is dosed it is then placed into an oven. In the oven, the mould rotates around two axes tumbling the powder. The rotation speed is relatively low around 20 revolutions per minute. As the mould becomes hotter the powder melts and sticks to the inner wall of the mould building up an even coating over the entire surface. After sufficient time to evenly distribute the molten polymer the mould is cooled using either air or water or a combination of the two. The polymer solidifies to the required shape. When the polymer has cooled sufficiently to retain its shape the mould is opened and the part removed.
The vacuum forming process involves the heating of a sheet of plastic until soft and then draping it over a mould. A vacuum is then applied which sucks the sheet over the mould so forming the desired shape. Where the shape is more complex or has deep recesses a plug may be used to assist the pressing of the plastic sheet into the mould. Once sufficiently cooled the part is then ejected and trimmed.
Some plastic parts can be produced by a variety of different moulding solutions. The decision on which method to use can depend on a number of factors including cost, quality of the finished part and dimensional tolerances needed. When considering cost, all factors should be taken into consideration. It may be that a single injection moulded part could combine a number of parts produced by another method, or result in a simpler assembly process thereby reducing costs. We have been in the plastic injection moulding business for over 65 years and have the experience and expertise to be able to advise you and ensure your part is optimised for manufacture.
Rutland Plastics is one of the leading plastic injection moulding companies in the UK. There are other thermoplastic moulding solutions available that are suited to different applications and each have their own advantages and disadvantages. Rutland Plastics is a plastic injection moulding specialist. Some of the other moulding solutions available from other companies are outlined below.
Injection blow moulding is used for manufacturing large quantities of hollow parts, e.g. bottles, jars and other containers. Molten plastic is injected into a hollow, pre-heated mould which forms the external shape. This is clamped around a core rod which forms the internal shape. The mould opens and the core rod is clamped into a chilled blow mould. The core rod opens allowing compressed air into the perform inflating it to the finished shape. Once cooled the mould opens and the finished item is stripped off the core rod.
There are a number of different methods of compression moulding but the process is broadly the same. The most common method is Dough Moulding Compound or Bulk Moulding Compound. The preheated material is placed directly into a heated mould. The material is forced into all cavities when the mould is closed with a top force. Heat and pressure are maintained until the material is cured. Another method is Sheet Moulding Compound, this process involves placing a reinforcing material, such as glass fibres, between layers of a thermoplastic and heating the materials so as to bond them together into a single sheet of material. This is then cut to size and reheated before being placed in a compression moulding press. This has a higher cost due to the handling and manufacturing costs in making the sheet. The material used in making the sheet is also heated three times – when making the initial thermoplastic sheet, then again when bonding with the reinforcement and finally, when making the part itself.
Rotational moulding (also referred to as Rotamoulding or Rotomoulding) is used to produce hollow plastic products. It differs from other moulding methods in that the melting and moulding stages occur after the polymer is placed in the mould and no external pressure is applied. A predetermined amount of polymer powder is placed in the mould. Once the mould is dosed it is then placed into an oven. In the oven, the mould rotates around two axes tumbling the powder. The rotation speed is relatively low around 20 revolutions per minute. As the mould becomes hotter the powder melts and sticks to the inner wall of the mould building up an even coating over the entire surface. After sufficient time to evenly distribute the molten polymer the mould is cooled using either air or water or a combination of the two. The polymer solidifies to the required shape. When the polymer has cooled sufficiently to retain its shape the mould is opened and the part removed.
The vacuum forming process involves the heating of a sheet of plastic until soft and then draping it over a mould. A vacuum is then applied which sucks the sheet over the mould so forming the desired shape. Where the shape is more complex or has deep recesses a plug may be used to assist the pressing of the plastic sheet into the mould. Once sufficiently cooled the part is then ejected and trimmed.
Some plastic parts can be produced by a variety of different moulding solutions. The decision on which method to use can depend on a number of factors including cost, quality of the finished part and dimensional tolerances needed. When considering cost, all factors should be taken into consideration. It may be that a single injection moulded part could combine a number of parts produced by another method, or result in a simpler assembly process thereby reducing costs. We have been in the plastic injection moulding business for over 65 years and have the experience and expertise to be able to advise you and ensure your part is optimised for manufacture.
RECENT POSTS
Free design guide
"*" indicates required fields