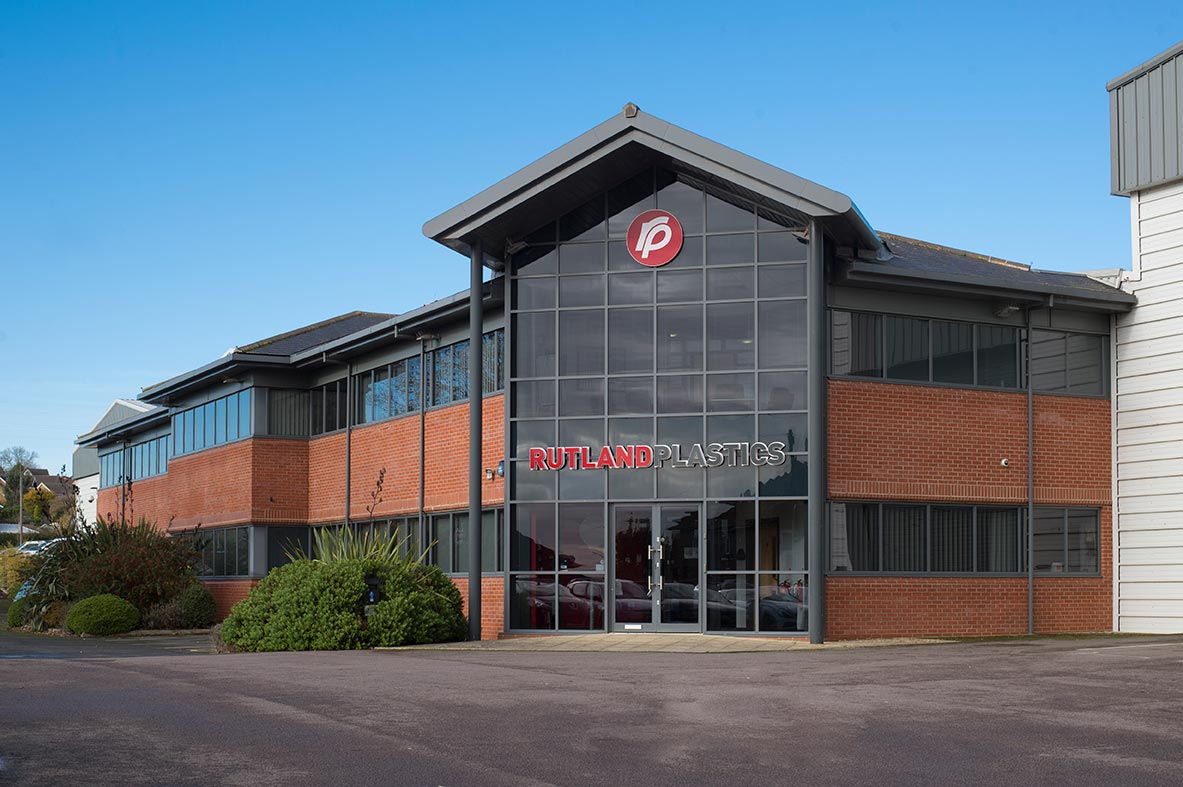
The plastic injection moulding process produces large numbers of high quality parts with great accuracy, very quickly. Plastic material in the form of granules is melted until soft enough to be injected under pressure to fill a mould. The result is that the shape is exactly copied. Once the plastic moulding has cooled sufficiently to harden the injection mould opens releasing the part. The whole injection moulding process then repeats.
The injection unit takes plastic raw material granules, heats them until molten, and injects them into the mould. Machines have a barrel that contains a screw, the barrel has heater bands around the outside which raises the temperature to the correct level to melt the plastic. This needs accurate control as different polymers have different melt temperatures, if the temperature is too low for the particular polymer then not all the material will melt. This will result in unmelted pieces of plastic being in the moulding affecting performance and appearance. Setting temperatures too high could result in the plastic degrading leading to poor appearance and reduced performance. The amount of time that the material resides in the barrel can also lead to degradation so weight of the part and cycle time become important factors.
The moulding machine itself illustrates how injection moulding works. The clamping end with moving platen takes half of the mould tool. This opens and closes the mould and supplies sufficient force to keep the mould closed when molten plastic is injected under pressure.
The rotating screw forces the plastic along the barrel. This in turn forces the screw back as the molten material collects at the end of the screw. When the right amount of material for the next shot has accumulated the screw stops rotating. The screw then acts like a plunger moving forward and forcing the molten plastic into the mould tool.
Moulding Process | Rutland Plastics
This animation shows, in simple terms, how the injection moulding process works. The final part of the process is the opening of the mould tool. The part is then ejected from the tool using either rods, a plate or an air blast. The process then repeats. The length of time from closing the injection mould to ejecting the finished plastic moulding is the cycle for the injection moulding of plastics.
The British Plastics Federation has information on injection moulding on their plastipedia site and there is more information on other aspects of injection moulding on our knowledge bank on our website
RECENT POSTS
Free design guide
"*" indicates required fields