WHAT IS THE INJECTION MOULDING PROCESS?
The plastic injection moulding process produces large numbers of parts of high quality with great accuracy, very quickly.
Plastic material in the form of granules is melted until soft enough to be injected under pressure to fill a mould. The result is that the shape is exactly copied. Once the plastic moulding has cooled sufficiently to harden the injection mould opens releasing the part. The whole injection moulding process then repeats.
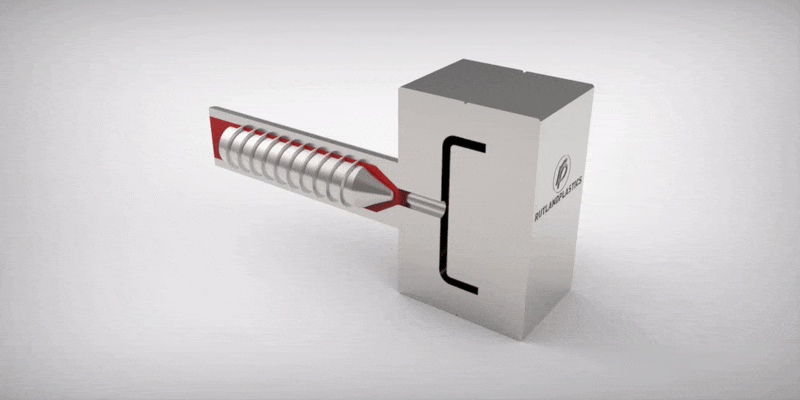
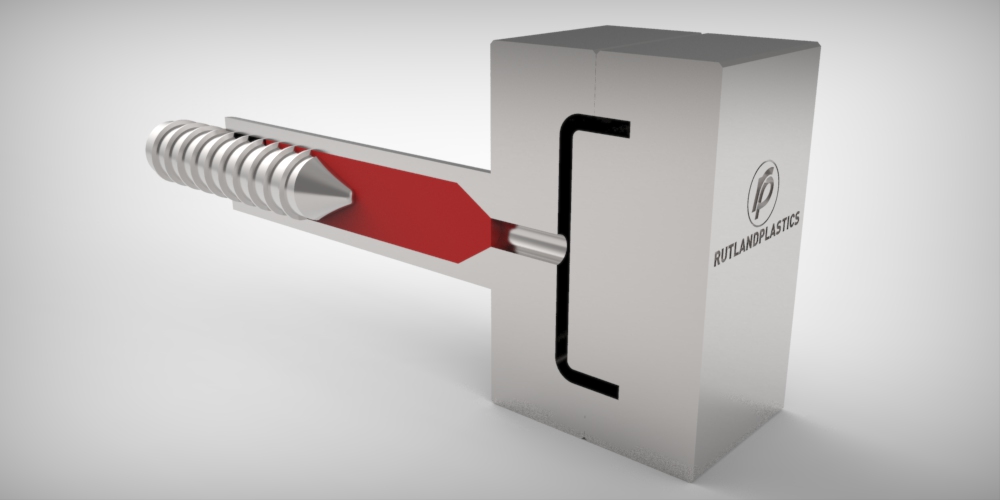
CLOSE MOULD
CLAMPING – the moving and fixed platens of the injection moulding machine hold the mould tool together under pressure.
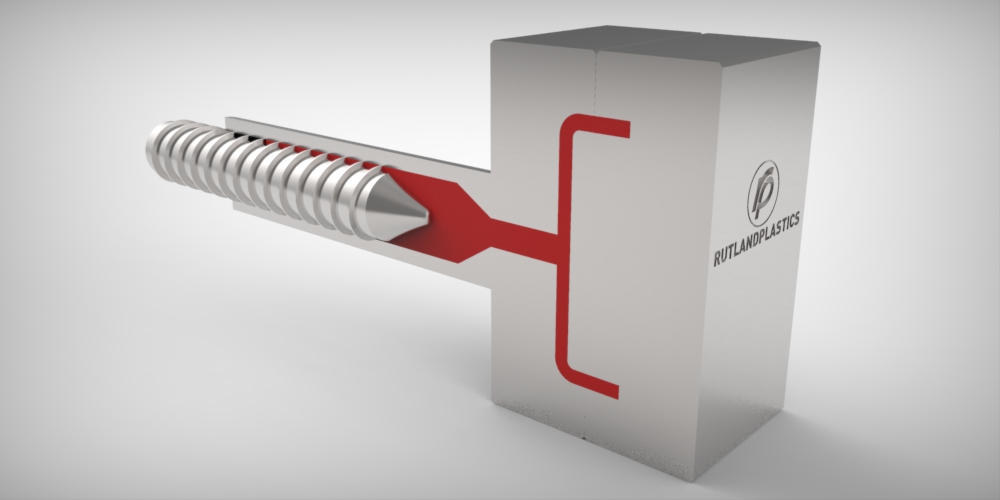
INJECT MOLTEN PLASTIC
INJECTION – the molten plastic that has been melted from pellet form in the barrel of the moulding machine is injected under pressure into the mould.
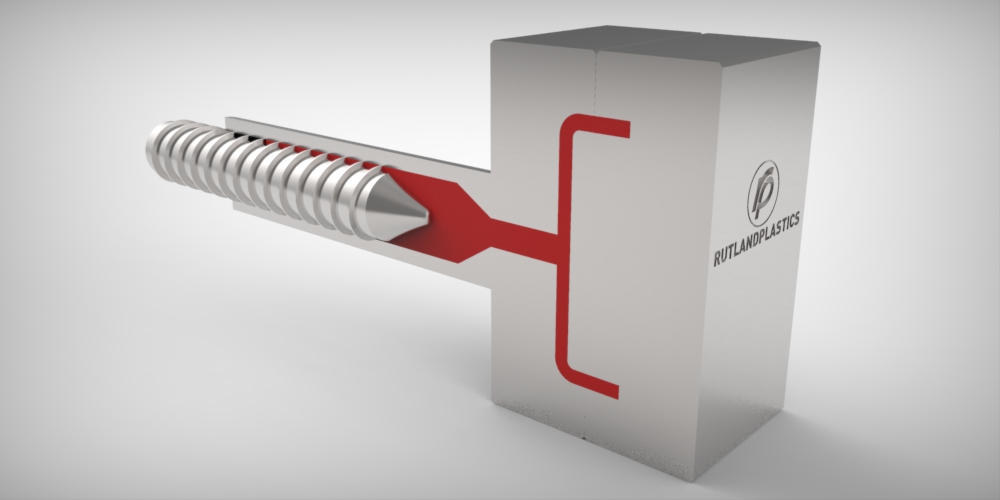
HOLD MOULD CLOSED
DWELLING – after the molten plastic has been injected into the mould, pressure is applied to ensure all cavities are filled.
COOLING – the plastic parts are then allowed to solidify in the mould.
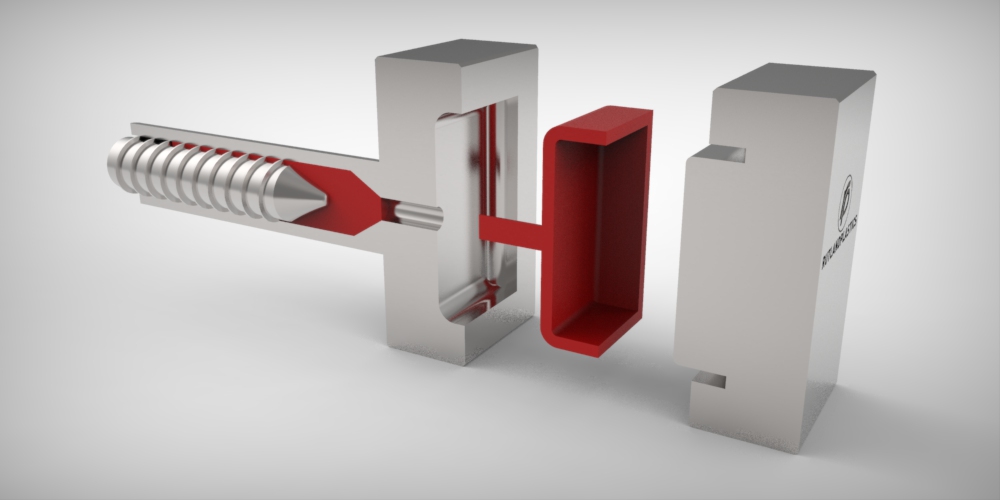
OPEN MOULD & EJECT PART
OPENING – the moving platen moves away from the fixed platen separating the mould tool.
EJECTION – rods, a plate or air blast then aids ejection of the completed plastic moulding from the injection mould tool.
The length of time from closing the injection mould to ejecting the finished plastic moulding is the cycle for the injection moulding of plastics.
You can read more about the moulding process in the following blogs 'How does injection moulding work', 'when is plastic injection moulding used' and 'what is plastic injection moulding'.