DESIGN FOR PRECISION
Plastic mouldings shrink on cooling which can present problems in part design. A thick section will either sink in so that the surface is not flat as designed, and/or there will be voids within the material mass.
This article is part of a series:
Design for Appearance
Design for Economy
Design for Recyclability
Design for Strength
Design for Stiffness
Design Summary
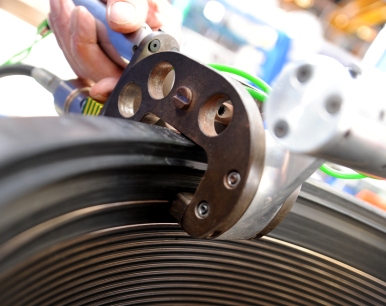
There are no specific rules on wall section but the following guidelines are often stated:
0.5mm – 5mm for unreinforced materials
0.75mm – 3mm for reinforced materials
However, do not be misled. There are circumstances when much thicker sections are required and can be moulded. Rutland Plastics are specialists in thick section moulding so contact us for advice. (see Thick Section Moulding).
WARPING
Frequently a part will shrink unevenly causing warping. Furthermore, parts may be heated during an assembly process, such as welding, or during curing following painting. This can cause both temporary and permanent dimension changes. Shrinkage also differs between in-flow and cross-flow.
SHRINKAGE FOR DIFFERENT MATERIALS
Amorphous materials exhibit lower shrinkage than semi-crystalline. Amorphous are the hard plastics, such as ABS, Polycarbonate, etc. Semi-crystalline are softer such as Polyethylene and Polypropylene.
Fillers also affect shrinkage – tending to reduce it.
WALL THICKNESS
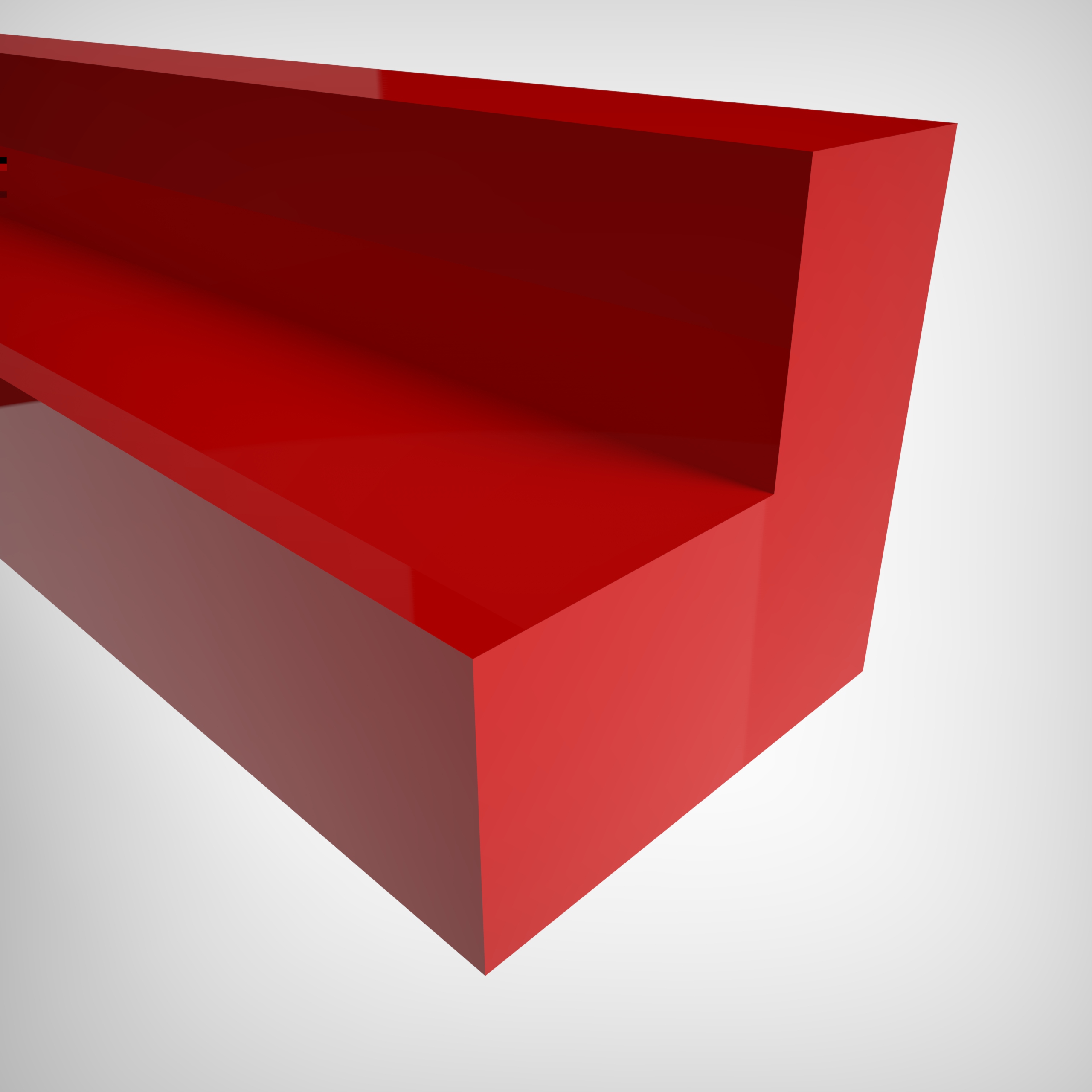
Wall thickness is a critical factor. Thin sections have a shorter cooling time so less opportunity for correction within the mould or by jigging. Varying thickness within a moulding also leads to distortion due to different shrinkages. If possible a gradual transition between different sections should be used.
However, this differential shrinkage could also be used as a means of correcting warping by thickening sections at appropriate points.
Ribs can also be a problem, especially where they have been made thinner to prevent sink marks as once again there are variations in the section. Gas injection or a blowing agent may be used to overcome the problem.
OTHER CONSIDERATIONS
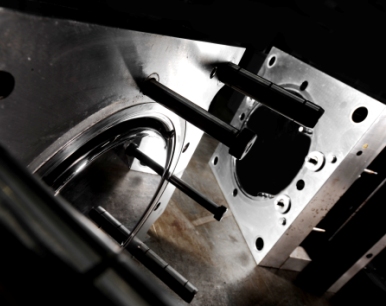
In addition to part design there are also a number of mould tool design and processing factors that need to be considered.
Tool design:
- Gate location
- Type and size of gate
- Cooling of the mould
- Ejection system
Processing:
- Melt temperatures
- Mould temperatures (each half of the mould can be a different temperature to help overcome warping)
- Filling, packing and holding pressures and times
- Post moulding jigs
FURTHER READING OR LINKS TO ALL GUIDES?
- Design Guide
- Design Development
- Design For Appearance
- Design For Assembly 1
- Design For Assembly 2
- Design For Assembly 3
- Design For Cost Consideration
- Design For Economy
- Design For Mouldability 1
- Design For Mouldability 2
- Design For Mouldability 3
- Design For Precision
- Design For Recyclability
- Design For Stiffness
- Design For Strength
- Design For Time
- Design Summary
- Flame Retardancy
- Flexibility
Free design guide
"*" indicates required fields