INJECTION MOULDING MACHINE
The injection unit takes plastic raw material granules, heats them until molten, and injects them into the mould. Machines have a barrel that contains a screw (imagine a kitchen mincer), the barrel has heater bands around the outside which raises the temperature to the correct level to melt the plastic. This needs accurate control as different polymers have different melt temperatures, if the temperature is too low for the particular polymer then not all the material will melt. This will result in unmelted pieces of plastic being in the moulding affecting performance and appearance. Setting temperatures too high could result in the plastic degrading leading to poor appearance and reduced performance. The amount of time that the material resides in the barrel can also lead to degradation so weight of the part and cycle time become important factors.
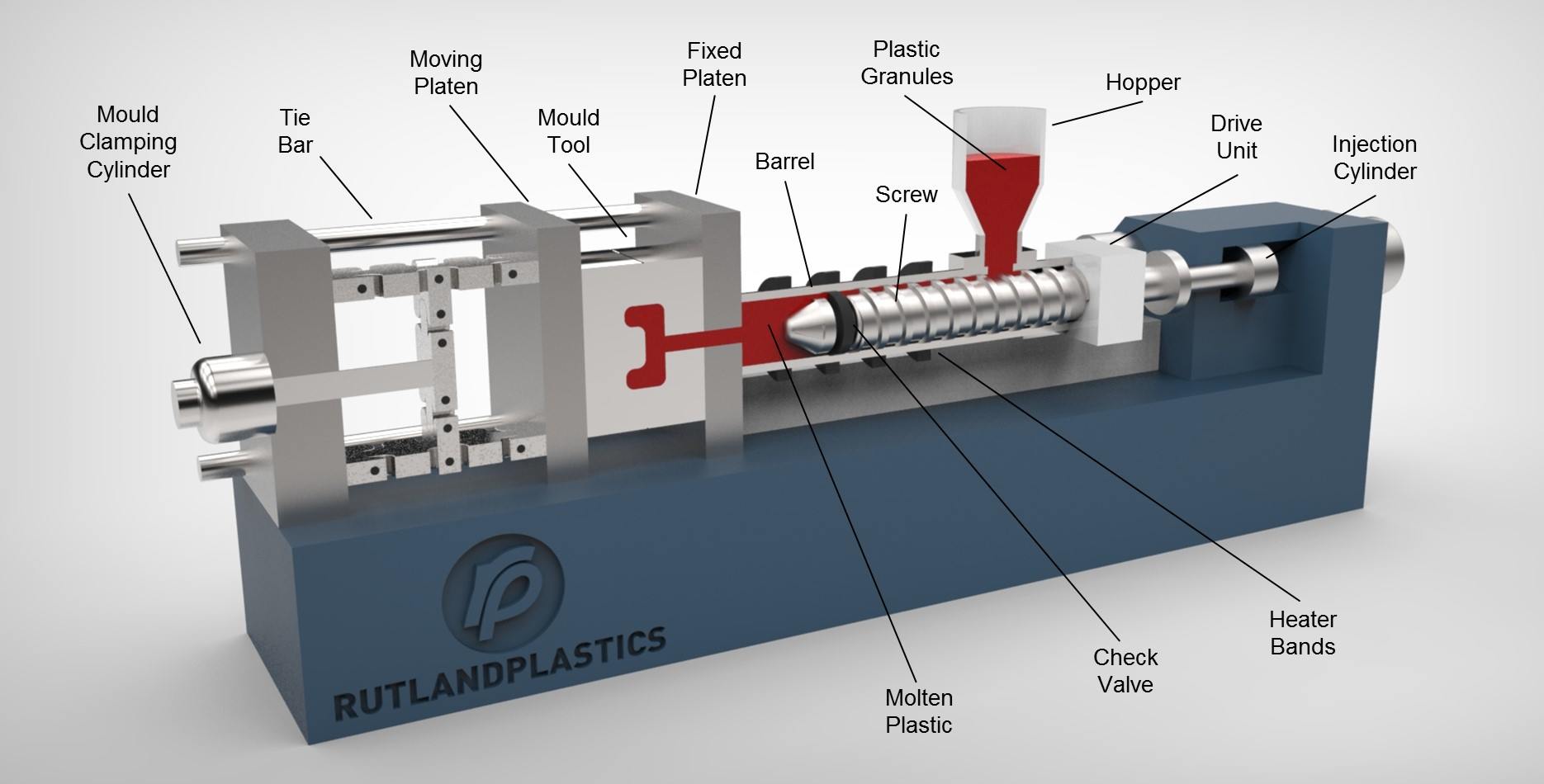
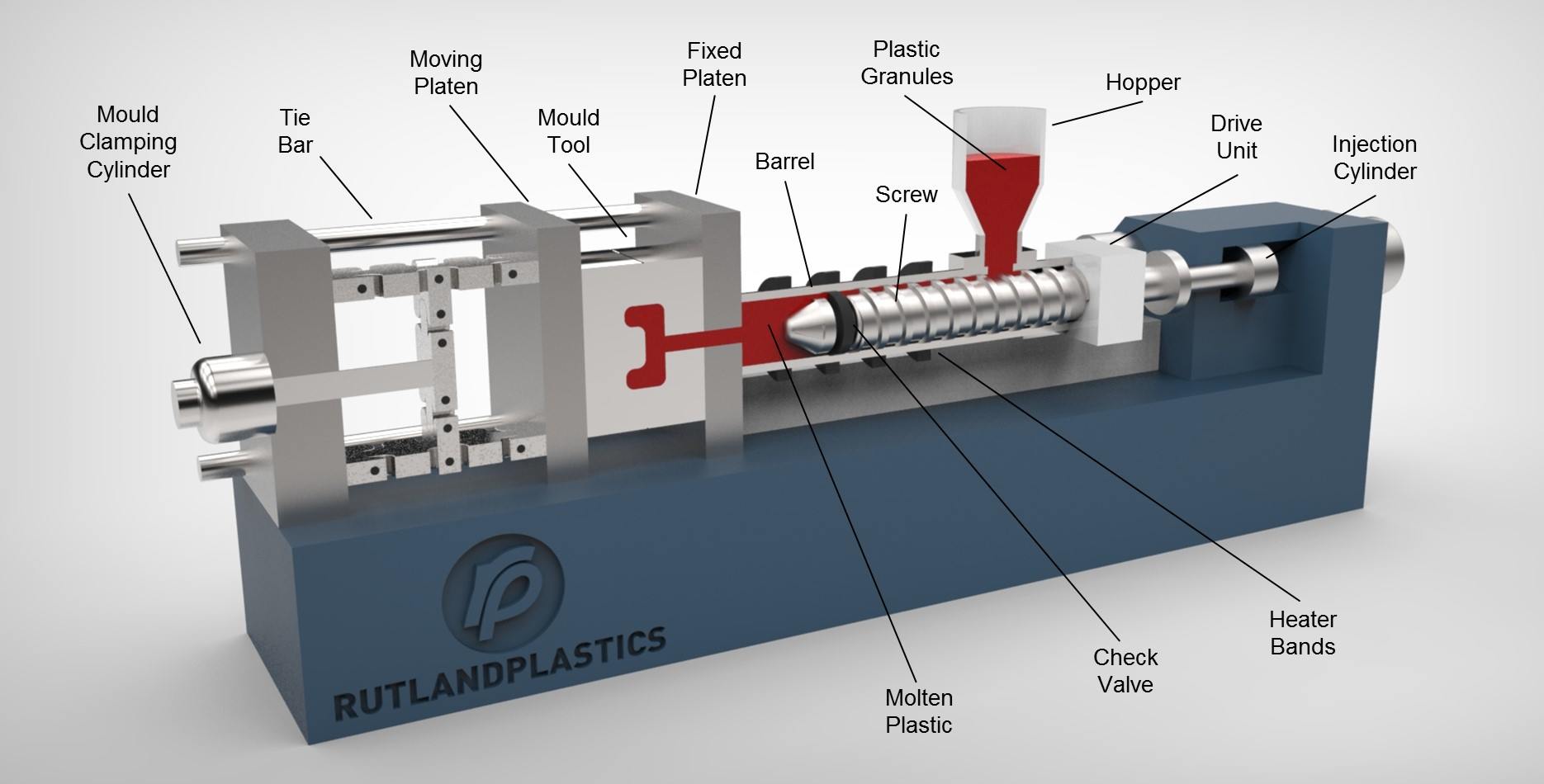
MOULDING MACHINE EXPLAINED
The clamping end with moving platen takes half of the mould tool. This opens and closes the mould and supplies sufficient force to keep the mould closed when molten plastic is injected under pressure.
The rotating screw forces the plastic along the barrel. This in turn forces the screw back as the molten material collects at the end of the screw. When the right amount of material for the next shot has accumulated the screw stops rotating. The screw then acts like a plunger moving forward and forcing the molten plastic into the mould tool.