GEARING UP FOR PLASTIC
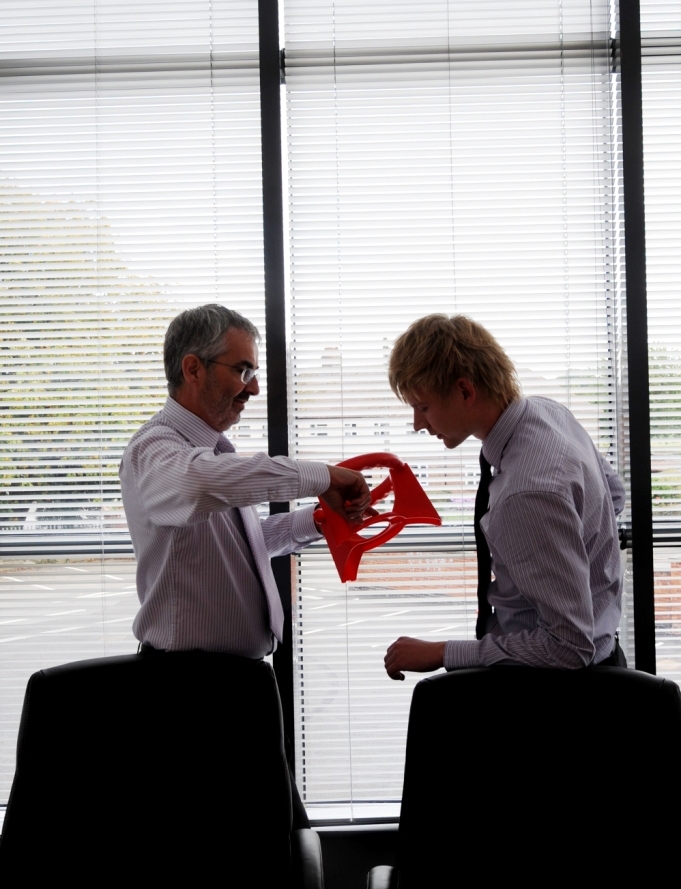
Demands for cost saving have led to engineering polymers replacing metals in many applications; one of these is the manufacture of gears. The range of products using plastic gears ranges from automotive applications, such as seat adjusters and windscreen wipers, through to domestic appliances and pumps, office equipment and power tools.
Initial developments in this field used the industry’s first engineering polymer – DuPont’s Zytel nylon. Today gears are manufactured from a range of engineering polymers depending upon the application.
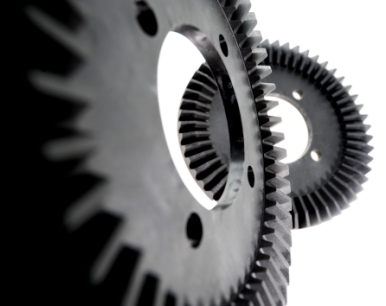
MATERIALS
Acetal (POM) – This is the most widely used. It is strong, tough, has a good surface hardness and fatigue endurance. Good resistance to moisture and chemicals and its natural lubricity reduces wear.
Nylon (PA) – This has excellent strength and toughness, as well as temperature resistance. Reinforced nylon can be used where better strength and stiffness are required. There are also high temperature grades, such as Stanyl PA46, that offer higher endurance and reduced dimensional change. This material can also be used in high torque transmitting situations.
Polyphenylene Sulphide (PPS) – Exceptional temperature and chemical resistance with good fatigue endurance. Effective in finely detailed parts under high loads. PTFE lubricated PPS grades have been used in automotive steering columns.
Polyester (PBT) – For strong, stiff gears in high temperatures (up to 150˚C). This material is not affected by moisture and has a high degree of dimensional stability.
Polycarbonate (PC) – Lubricated polycarbonates can be used for highest accuracy.
Thermoplastic Elastomer (TPE) – For low noise gear trains.
Liquid Crystal Polymer (LCP) – For extremely small or thin gears under light loads, such as wristwatch gears. Ultra high temperature resistance with superior chemical resistance and dimensional stability.
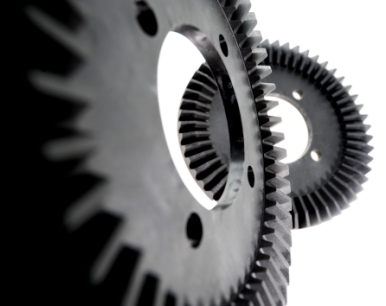
WHY PLASTICS?
There are many advantages of polymers for gears:
- Low coefficient of friction, particularly important if lubrication is not possible. Some polymers also have added internal lubricant.
- Superior shock resistance. Polymers are better than metal at absorbing shock and impact. Toughened grades are also available for more demanding applications.
- Polymer gears are quieter im operation than their metal counterparts. This can be particularly important in office equipment or domestic appliances.
- Plastic gears can mate with metal gears as well as other plastic gears, manufactured from the same polymer or a different one. Wear of plastic against steel is generally lower than against another plastic.
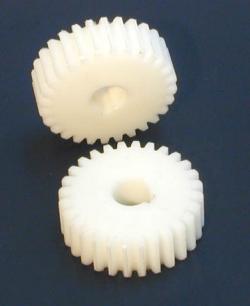
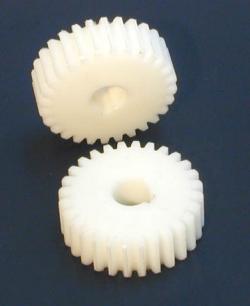
WORKING EXAMPLES
A couple of applications will serve to illustrate the benefits of plastic gears.
A popular example of the use of polymer gears is the Maytag washer transmission. Changing to polymer gears saved 6kgs and eliminated 42 parts. Gears were moulded in glass fibre filled and unfilled acetal.
Whirlpool washing machines introduced a splined clutch, also using gears made from acetal. The low wear properties meant that this assembly lasts four times the projected life of the washing machine. It also reduced the number of moving parts by 20%.
The weight savings can be considerable, bearing in mind that the S.G. of steel is 7.85 against around 1.40 for glass filled nylon and acetal.
For further information: